|
|
石英加工厂制备高纯超细石英粉所需工艺及注意事项 |
来源:中国粉体技术网 更新时间:2014-07-31 09:24:01 浏览次数: |
|
|
石英粉是一种优质的中性无机填料,广泛应用于塑料、橡胶、涂料、电子及高科技产品等行业。尤其是现代电子工业的飞速发展,半导体器件封装材料中需要大量使用的环氧塑封料的主要填料就是高纯超细石英粉(SiO2含量大于99.95%,d50为2~5µm)。
高纯超细石英粉具有介点性能优异、热膨胀系数低、热导率高、及相对于环氧树脂价格低等特点,可以使封装材料热膨胀系数、吸水率、成型收缩率及成本率降低,耐热性能、机械强度、介电性能及热导率提高等特点。
我国是世界硅质原料矿产大国,石英岩、石英砂岩、脉石英、粉石英、石英砂等硅质原料矿床在我过已成规模的开发,但高品位的矿床(SiO2 含量大于99.95%)却相当稀少。国外高纯超细石英粉的生产,也是利用同样的原料,进行深度选矿提纯,超细粉磨精制而成的。
随着国内电子封装行业的发展,高纯超细石英粉的需求量越来越大。一方面是厂商大量的从国外高价进口高纯超细石英粉,另一方面却是我国广大中小型石英粉加工厂因技术限制只能生产价格低廉的石英粉。如何解决这对矛盾,是值得我们认真思考的问题。本文主要介绍以脉石英、石英岩为原料的中小型石英加工厂在加工高纯超细石英粉过程中应该添加的工艺,以及值得注意的事项。
1 硅石的破碎,磨碎和超细粉碎
1.1 热力破碎
硅石的硬度大,若沿用其他矿物直接进行破碎的方法,能耗高、效率低。故可首先进行热力破碎。热力破碎,即:煅烧-水淬法。它是利用硅石经过高温煅烧(900~1150℃设施度),用水淋冷却(最好不用水池。因为水池冷却时,在硅石表面可形成大量的水蒸气泡。与液体水相比,不易导热,即不易形成“急冷”的效果)硅石在急剧的由“热胀”,到“冷缩”,在其表面和块体内部产生大量的微裂纹,从而使硅石强度大幅下降(降到原来的1/10)的一种方法。它的优点是:可以大大提高破碎效率、减少设备故障率、降低破碎成本。
经过试验,得出如下技术指标:入窑粒度20~75mm,窑内容积38m3,生产能力8t/h,重油耗量19.64kg/t矿石,单位电耗7.38kw·h/t,单位水耗:0.5t/t矿石。虽然煅烧硅石需要增加能耗,但是由于处理后的矿石机械强度大大降低,这样可以减少机械铁屑的混入;在工艺上也可以减少破碎段数、减少衬板、磨矿介质及其他部件的损失,降低成本。并且可以打开部分硅石中的包裹体,使包裹体中的杂质露出来,有利于后续的“酸洗除杂”工艺,减少酸耗。
1.2 粉碎机械的选型
由于工业上对超细粉体材料的大量需要,出现了各种超细粉体加工机械。振动磨、搅拌磨、气流磨,是目前国内常用的超细粉碎机械。各种磨机都有其特点。
振动磨是利用振动筒体,来使磨介做高频振动对物料进行粉碎的。适用于各种硬度脆性物料的细磨与超细粉磨。只要对磨介级配、物料含量、振动频率、振幅等条件进行合理控制,可生产亚微米级粉体。缺点是由于需要震动筒体,因而对机械振动强度要求较高,不能做得很大。一部分能耗用在振动筒体和磨介上,能量利用率有限。
搅拌磨则是利用搅拌浆击打磨介,使磨介与物料做循环运动和自转运动,在筒体内不断的与物料进行摩擦、冲击、剪切作用而使之粉碎。采用合适条件也可以生产亚微米级的粉体。由于其不需要振动筒体,而是将能耗绝大部分用于直接搅动磨介,因而与球磨,振动磨比起来能耗都要低。它分立式和卧式两种:卧式可以做得很大,但是出料较难。立式则不能做得太高,否则底层磨介受高压易于破裂。
气流磨常被用做精细化工、药物等干性产品超细粉碎。它的优点是没有磨介对物料的污染,但粉碎功耗大、粉碎物料硬度要求低、一般产品附加值较高时才采用。
对于超细石英粉而言,常采用搅拌磨和振动磨。对于磨介的要求是选用磨耗少、硬度高,直径大小为1~5mm之间。可以不同规格的磨介进行搭配使用,为防筒内壁机械铁的污染和损耗,可用离心的办法做成高耐磨的聚酯筒壁。
1.3 超细石英粉的加工工艺
目前中小型石英粉加工厂生产工艺现状,很多是干法生产。干法生产石英粉的优点很明显:综合生产成本低、产量高、工艺容易控制。但是缺点也很明显:车间粉尘太大、有粉碎极限(较难生产微米级石英粉)。生产超细粉体时,一般采用湿法工艺。并且,一般制备高纯石英粉需要浮选、酸洗除杂,这样更应采用湿法工艺。一般的工艺流程为:(原有工艺生产的矿粉)-磁选(除铁)-浮选(除铝)-超细粉磨(粒径5µm,2500目以上)-酸洗(除铁)-脱酸清洗-压滤脱水-烘干-打散-成品。可以对磁选和浮选的位置做适当编排修改。
1.4 助磨剂
助磨剂是一种能够加速物料粉磨过程,提高粉磨效率,降低能耗的一类物质。一般来说,助磨剂都是一种表面活性剂。添加入物料中,可以吸附在物粒的表面上,与颗粒发生物理或化学的作用,产生力学效应,最终加速物料的粉碎。添加助磨剂的另一个原因,是由于一般超细粉碎都有一定的粉碎极限。即:无论多长时间,都无法磨至某个粒度以下,并且随着时间的推移,颗粒由于团聚作用,粒度反而会增大。添加助磨剂可以降低颗粒的表面能,使颗粒“解散”,粉磨得以向更小的粒度方向发展。超细粉碎是一个高能耗的工艺段。添加助磨剂有利于降低能耗。表1给出文献中报道过的对石英有助磨作用的物质。
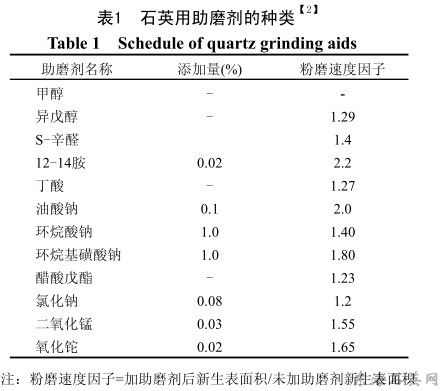
2 石英粉的选矿提纯
不同的硅石,其二氧化硅品位有高有低。总的来说,以石英为主,其次是各种长石岩屑、重矿物(石榴石、电气石、辉石、角闪石、黄玉、绿帘石、钛铁矿等)以及云母、绿泥石和粘土矿物等。制备高纯度(99.95%以上)石英粉,一般来说,是选用纯度较高的脉石英和石英岩作为原料,将其破碎到一定程度后,进行选矿提纯的。石英粉的选矿提纯视其中杂质Al2O3、Fe2O3和Ti、Cr的含量为主要工作内容。并视其中的含铁杂质和含铝杂质为石英粉纯度质量的主要考核指标。国际国内市场不同纯度的石英粉体价格差异很大。通常不经过选矿提纯的原矿块矿售价仅100~200元/t,但是高纯度的石英原料价格要高出数十倍。随着电子工业的飞速发展,高纯度石英粉供不应求,选矿提纯在提高产品价值方面有重要意义。
2.1 含铁杂质的脱除
铁在硅质原料中常以以下几种形式存在:①以微细粒状态赋存在粘土,或者高岭土化的长石中;②以氧化铁薄膜形式附着在石英颗粒的表面;③含在重矿物和褐铁矿、磁铁矿、钛铁矿、黄铁矿等颗粒中;④铁呈次要成分存在黑云母、角闪石、石榴子石等矿物中;⑤在石英颗粒内部呈浸染或透镜状态;⑥以固溶态存在于石英晶体内部。此外,加工过程中也会混入一定量的机械铁。
对于不同形式的铁杂质,宜选用合适的选矿方法 。对于处理以细微颗粒状存在于粘土矿物中的铁时,一般可用水洗和脱泥的方法。硅质原料中,SiO2的品位随着硅制原料的粒度的变细而降低,而铁品位正好相反。所以,脱泥可以降低铁杂质的含量。
脱除石英颗粒表面薄膜铁或者铁锈,可以采用擦洗和化学酸浸方法处理。擦洗可以进一步擦碎未成单体的矿物集合体,再经过分级作业达到对原料的进一步的提纯效果。目前,主要有棒磨擦洗和超声波擦洗。对于机械擦洗法,主要影响因素是来自擦洗机的结构特点和配置形式,其次为工艺因素。主要包括擦洗时间和擦洗浓度。研究表明,砂矿擦洗浓度在50%~60%之间效果最好,擦洗时间原则上以初步达到产品质量要求为准。时间过长,会加大设备磨损,增加成本。
除采用擦洗法除铁,还常采用酸洗除铁工艺,去除颗粒表面薄膜铁。酸处理常用酸类有硫酸、盐酸、硝酸、醋酸和氢氟酸。还原剂有亚硫酸及其盐类等。上述酸类对石英中的非金属杂质矿物均有较好的去除效果。各种稀酸对Fe和Al的去除效果明显,而对Ti和Cr的去除则主要利用较浓的硫酸、王水和氢氟酸处理。影响酸处理效果的主要因素是酸浓度、温度、时间、以及洗涤过程等。
以安徽某地石英岩为例,采用氢氟酸,硫酸,盐酸混酸法,制得纯度为99.99%的高纯度石英。并且指出,若要制得高纯度石英产品,氢氟酸的加入是高品位产出的保证。由于氢氟酸有剧烈的毒性,加入量不应超过10%。太多则对石英的侵蚀过大,产率过低。太少则不能完全将石英包裹体打开,使酸无法与包裹体内杂质充分接触反应,达不到提纯效果。
对于含铁重矿物,一般可以采用重选和磁选的方法清除。重选常用设备为螺旋选矿机、溜槽和摇床等。一般来说,摇床除铁钛优于螺旋选矿机。若粗选和精选作业条件控制适宜,精矿Fe2O3含量可以降低到0.05%左右;但是摇床占地面积大,处理能力低(一般处理量为数百kg/h)而且耗水量大,操作条件复杂,不宜用于低附加值的石英生产。磁选用弱磁磁选机除去磁铁矿,用强磁磁选机选出钛铁矿、褐铁矿、赤铁矿、石榴子石等磁性矿物。对于含铁矿物粒度较细者,更多可采用浮选法分离。
2.2 含铝杂质的脱除
硅质原料中的含铝杂质主要来自长石、云母和粘土矿物。对于粘土矿物,采用擦洗和分级脱泥流程去处理,而对于存在于长石和其他矿物中的氧化铝,则主要采用浮选法。另外,浮选也可以除去粗磨时混入的铁质杂质。
浮选是利用矿物和杂质表面性质不同,通过添加各种捕收剂,起泡剂,表面活化剂来控制矿物与杂质表面的疏水性或亲水性,从而使矿物得到分离的选矿方法。由于原料中二氧化硅含量一般在98%以上,故常采用反选法,以硫酸为矿浆pH值,控制石英表面电性,以氢氟酸为活化剂,选用胺类阳离子捕收剂。长石类杂质主要存在于浮起物中,可除去。剩下即为石英精矿。
由于氢氟酸有剧毒,对环境和设备有很大的损害,故人们开始尝试采用无氟工艺。以江西上饶某地脉石英为原料,矿浆浓度为20%,先用10%的硫酸调整矿浆pH值为3,然后按400g/t加入十二胺醋酸盐进行浮选,除铝率接近70%,效果较好。
3 石英粉的表面改性
用于高分子填料用的石英粉及其他形式的二氧化硅粉体,为了使其表面与高聚物基料相容性好,使填充材料的综合性能及可加工性能得到提高和改善,必须对其进行表面处理。常用的是各种硅烷偶联剂。它能降低石英粉体的表面能,提高与高聚物基料的润湿性,改善粉体与高聚物基料的相容性。此外,这种新表面的形成,可以改善填充复合体系的流变性能。
影响石英粉表面处理效果的主要因素有:硅烷偶联剂的品种、用量、使用方法以及处理的时间、温度、pH值等。
根据分子结构的不同,硅烷偶联剂可以分为氨基硅烷、环氧硅烷、硫基硅烷、甲基丙烯酰氧基硅烷等品种。用于环氧树脂填料用石英粉的硅烷偶联剂,常选用氨基硅烷、甲基丙烯酰氧基硅烷等。商品型号为KH550、KH560、KH570等。这些硅烷偶联剂的官能团能够跟环氧树脂有良好的适用性。
应用硅烷偶联剂的方法主要有两种 :一是将硅烷偶联剂配成水溶液,用它处理石英粉后再与有机高聚物混合,即预处理方法;另一种方法是将硅烷偶联剂与石英粉及有机高聚物基料混合,即迁移法。前一种方法的表面处理效果较好,是常用的表面改性方法。
硅烷偶联剂在使用前一般都要配成水溶液,即使其预先水解。水解时间随品种、溶液的pH值不同而不同,从几分钟到几十分钟不等。其水溶液的pH值一般在3~5之间。即配即用。硅烷偶联剂的用量,与偶联剂的品种和石英粉的比表面积有关。一般硅烷偶联剂的用量选定为石英粉质量的0.10%~1.50%。具体用量需要进行试验才能确定最佳值。
石英粉的选矿提纯和超细粉碎是很有经济效益和应用价值。以增加选矿提纯工艺段为例,吨成本可以控制在1000元到2000元之间,而SiO2含量大于99.99%的石英价格在8000元以上。粒径47µm(325目)石英粉每t价格在280~320元之间,但粒径10µm(1250目)即可达2500元。随着目数的增加,其价格也与同粒径的重钙粉、滑石粉相差越来越大。随着微电子、光电等行业的发展,高纯超细石英粉的优良性能是其他超细粉末所无法替代的,市场前景极为广阔。
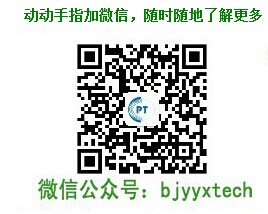
|
|
|
|
|
|
|
|
|
|
|
|