光电分选是根据矿物表面光学特性的差异,对石英矿物和杂质矿物进行初步粗选的方法,它对粗粒级的矿物分选有显著的效果。
根据能抛早抛的原则,色选一般设置在磨矿之前,利用色选可初步将石英矿石分成几个等级,分别加工利用,以便更加合理地开发利用石英资源,可提高精矿品位和选矿回收率,大大降低消耗。
1、石英砂色选原理
色选机是根据物料光学特性的差异,利用光电探测技术将颗粒物料中的异色颗粒自动分拣出来的设备。色选机主要由给料系统、光学检测系统、信号处理系统和分离执行系统组成。
石英砂原矿中,较纯的石英砂为白色或乳白色,含铁杂质或其脉石矿物的颜色则微黄、浅黄色或浅褐色和灰色等,石英砂与含铁杂质或脉石矿物的颜色差异是色选的关键。
2、不同粒级石英砂的色选特点
石英砂色选范围主要集中在对原矿石3-8cm颗粒的色选,0.5-3cm颗粒的色选和4-140目颗粒的色选。不同粒级的石英砂色选效果会受到多种因素影响。
(1)大粒度石英砂
由于颗粒较大,与色选机的接触面积相对较大,光学检测系统更容易捕捉到其表面的杂质和色差。而且大颗粒在输送过程中稳定性较好,不易发生滚动或堆积,能更准确地被检测和分选。例如在建筑用石英砂的生产中,大粒度石英砂经过色选后,能有效去除其中的黑色、黄色等杂质颗粒,提高石英砂的纯度和外观质量。
(2)中粒度石英砂
中粒度石英砂的色选效果相对较为平衡,既不像大粒度石英砂那样容易检测,也不像小粒度石英砂那样存在检测难度。在色选过程中,需要色选机的光学系统和检测精度达到一定水平,才能较好地分辨出杂质颗粒。比如在一些对石英砂纯度要求不是极高的工业应用中,如普通玻璃制造等领域,中粒度石英砂经过色选后,能去除大部分明显色差的杂质,满足生产需求。
(3)小粒度石英砂
由于颗粒细小,容易相互粘连或堆积,影响光学检测系统的成像和检测精度。而且小颗粒在输送过程中稳定性较差,容易受到气流、振动等因素的影响,导致检测和分选的准确性降低。不过,随着色选技术的不断发展,一些先进的色选机通过优化光学系统、提高检测精度和采用特殊的输送方式,也能对小粒度石英砂进行有效的色选,如在电子级石英砂的生产中,对小粒度石英砂进行精细色选,以去除其中的微量杂质,但可能需要色选2遍以上才能处理干净。
(4)粒度分布均匀的石英砂
如果石英砂的粒度分布较为均匀,即不同粒级的石英砂比例相对稳定,那么在色选过程中,色选机的处理量和色选精度相对容易控制。因为均匀的粒度分布使得石英砂在输送和检测过程中更加稳定,减少了因粒度差异导致的检测误差和分选困难。例如在一些大规模的石英砂生产线上,通过筛分等预处理工艺,将石英砂分成不同粒度级,然后对每个粒度级分别进行色选,可以提高整体的色选效果和生产效率。
(5)粒度分布不均匀的石英砂
当石英砂的粒度分布不均匀时,可能会出现大颗粒和小颗粒混合的情况。大颗粒可能会遮挡小颗粒,影响小颗粒的检测和分选;小颗粒可能会附着在大颗粒表面,导致色选机误判。此外,不均匀的粒度分布还可能使色选机的处理量不稳定,影响生产效率和色选效果。比如在一些小型石英砂加工厂,由于设备和工艺的限制,石英砂的粒度分布往往不够均匀,需要在色选前进行充分的筛分和预处理,以提高色选效果。
3、色选机的考察指标
(1)处理量
处理量即每小时可处理的物料数量,影响单位时间处理量大小的因素主要是伺服系统的运动速度、传送带的最高速度和原材料的纯度。伺服系统运动速度快,就能很快地把执行器送到杂质对应的位置,也就可以提高传送带的速度,增加处理量,反之就要减小传送带速度。单位时间处理量与传送带的运动速度成正比,传送带速度越快,产出量就越大。单位时间处理量与原料所含杂质的比例大小也相关,如果杂质很少,两个杂质间隔越大,留给伺服系统的反应时间就越长,也就可以增大传送带的速度。同时单位时间处理量与所要求的选出精度密切相关。
(2)色选精度
色选精度是指从原料中选出的杂质数量占所含杂质总量的百分数。色选精度主要受传送带的运动速度和原料的纯度有关,传送带运动速度越慢,相邻杂质之间的时间就越长,伺服系统就有足够的时间将杂质剔除,提高色选精度。同理原料的初始纯度越高,杂质量越少,色选精度就越高。同时色选精度还受到伺服系统自身设计限制,当有两个以上杂质处在同一帧图像时,只能剔除一个杂质,色选精度下降,采用复选结构要好于单选结构。
(3)带出比
带出比是指色选机选出的废料中杂质数量与正常物料数量之比。带出比的高低是可以调节的,主要依靠调节执行器的通电时间来完成带出比的调节。如果带出比设定过高,会影响选出率和处理量这两个指标;如果设定过低,选出的废料中所含正常物料过多,会造成浪费;如果再处理,需要投入一定的人力和物力,会造成很多的麻烦和经济损失。
实际生产过程中,处理量、色选精度和带出比这三个指标是一体的,都是关键指标,必须同时考察。
4、石英砂色选技术要点
(1)色选效果影响因素
相机分辨率、软件算法、喂料系统、喷嘴工作性能等是影响色选效果的重要因素,当然还有一些综合性的因素,比如:在软件的升级和喷阀的反应速度同时满足的情况下,伺服系统的运动速度、传送带的最高速度和原材料的纯度则会影响色选精度和单位时间处理量大小;另外,有些厂家在实际分选过程中,将坏料循环分选,大大减少了矿石成品率,在有效的时间内降低了合格品的效率,导致带出比提高。但如果带出比设定过高,会影响选出率和处理量这两个指标;如果设定过低,选出的废料中所含正常物料过多,会造成浪费。
(2)调试技巧
综合来讲,提高灵敏度,色选效果就越好,带出比就会越大;而产量要求也是直接影响色选效果和带出比。色选机的腹带速度也一个重要指标。有些厂家在不能解决履带速度问题,只能加大物料的覆盖率,在现场生产中,这样的覆盖率会严重缩小物料之间的有效距离,在分选中就会降低分辨率,导致很多坏料“逃之夭夭”,因此,这样的方式只会使物料的带出比加大,更降低了选净率。长期下来,对于矿业生产厂商,根本达不到生产要求,更别说回收成本,增加效益了。
如果达不到预期的色选效果,除了调试不当外,还有一点影响因素便是原料的含杂率。含杂率低的情况下,杂质之间间隔大,留给伺服系统的反应时间长,也就可以增大传送带的速度,提高产量。同样的,原料的初始纯度越高,杂质量越少,色选精度也就越高,精度越高,产量就越高。而原料中正常物料和瑕疵物料必须存在一定的色差;色差越小,色选难度越大,性能指标也越差,对不同颜色的物料的选出率也不同。
(3)色选精度把控
对质量影响最大的因素就是色选的精度,对物料成品要求高的一般都要做到色选精度高。
以石英砂为例,倘若是生产板材砂,就必须是高纯度的,石英砂的表面上不能有一点点的黄皮,石头的硬度也要好,这样做出来的石英板材才能满足业内的标准。若是生产高纯石英砂则质量要求就更高了。
相反的,若是用于普通玻璃、涂料、橡胶、塑料等领域中的填料用石英砂,则对质量要求相对没那么高,有一定的掺杂率也不影响应用,便可适当的追求产量。
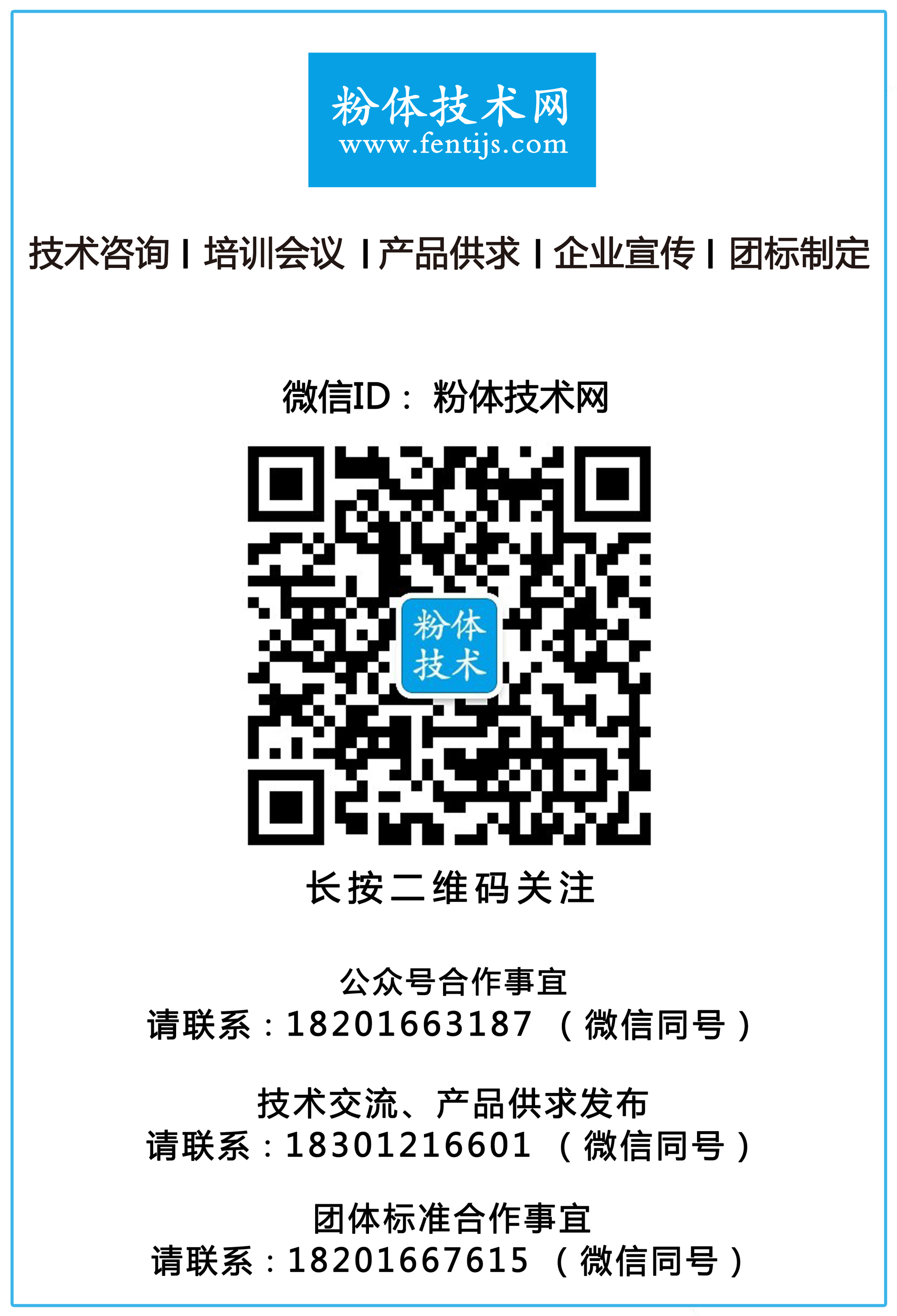
|