我国是硅石矿产大国,多种硅质原料矿床在我国已成规模开发,但高品位的矿床( SiO2含量>99.95%) 却相当稀少。高纯石英是由硅质原料深度选矿提纯而成,广泛应用于各种玻璃、微电子塑封料填料、机械铸造、冶金和化工等领域。
随着国民经济和科学技术的飞速发展,硅质原料更多地开始应用于高新技术产业领域,如半导体封装材料、SiO2薄膜材料、光纤通讯电缆材料及航空航天等。这些领域对石英砂质量有很严格的要求,一般要求SiO2的含量在99.9% 以上( 见表1) 。由于这些行业关系到国家的长远发展,因此高纯石英的战略地位非常重要。
原料预处理
石英煅烧水淬处理( 也称热力破碎) ,是指石英在高温煅烧时会发生晶形转变( α 石英→β 石英→β鳞石英) ,从而使体积增大,晶体中原有的缺陷程度变得更严重,当水淬时晶体体积突然变小,晶体缺陷处的内应力迅速增大促使晶体在缺陷处破裂的一种方法。晶体在缺陷处破裂,使原石英中的包裹体和裂隙中的杂质暴露在颗粒表面,酸处理时就能易于除去。试验表明在同样试验条件下经煅烧水淬处理后的样品比不处理的样品在酸处理时除杂率能提高5% ~ 10%。
对于超细石英粉而言,常采用搅拌磨和振动磨。对于磨矿介质的要求是选用磨耗少、硬度高,直径大小为1 ~ 5mm,可以不同规格的磨矿介质进行搭配使用,为防止筒体内壁机械铁的污染和损耗,可用离心的办法做成高耐磨的聚酯筒壁。在超细粉碎过程中应添加适量助磨剂( 一种表面活性剂) ,可降低颗粒的表面能,加速物料的粉碎,提高粉磨效率,降低能耗。对石英有助磨作用的物质见表2。
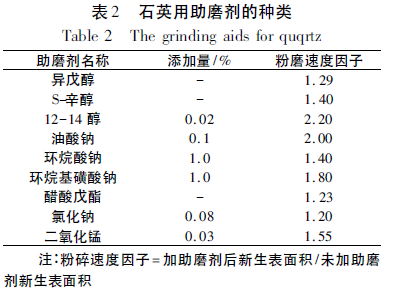
高纯石英制备技术
石英中的杂质主要为氧化铁及氧化铝等金属氧化物,其中,部分Fe2O3以氧化膜的形式附着在石英颗粒表面,Al2O3则以黏土矿物( 如高岭土、伊利石、云母等) 的形式混入。因此,石英砂提纯方法及工艺流程的技术进步和发展也主要体现在对铁质和铝质的有效脱除上。
石英提纯工艺主要分为初提纯和精提纯两大类,高品位SiO2矿石初提纯最常采用的是磁选法和浮选法。磁选的目的是除去原料中的磁性矿物,如褐铁矿、钛铁矿、磁黄铁矿和石榴子石等,也可除去带有磁性矿物包裹体的颗粒。浮选的目的是除去与石英伴生的矿物长石、云母、高岭土等。经除铁、铝为主的初提纯工艺方法的处理,SiO2含量99% 以上石英矿石中的强磁性杂质矿物和加工中带入的机械铁即可除去。精提纯主要是采用化学方法进行,使物料中杂质组份的化学组成发生变化,并进行分离。
2. 1 初提纯选矿工艺
擦洗
擦洗是借助机械力和砂粒间的磨剥力来除去石英砂表面的薄膜铁、粘结及泥性杂质矿物和进一步擦碎未成单体的矿物集合体,擦洗可以擦碎未成单体的矿物集合体,再经过分级作业达到对原料的初步提纯效果。目前,主要有机械擦洗和超声波擦洗。影响机械擦洗法效果的主要因素是来自擦洗机的结构特点和配置形式,其次为工艺因素( 主要包括擦洗时间和擦洗固体浓度) 。研究表明,石英砂矿擦洗固体浓度在50% ~ 60% 之间效果最好,擦洗时间原则上以初步达到产品质量要求为准。时间过长,会加大设备磨损,增加成本。
超声波擦洗是用超声波对液体中的石英颗粒进行猛烈冲击,从而使颗料表面的微量杂质或水化膜迅速地从石英颗粒表面剥落,在分散剂的作用下成为微细的悬浮物,脱离石英砂,经洗涤分离后,使石英砂纯度大大地提高。
根据廖青、朱建军等的研究,水和少量分散剂的液体介质中,经超声波处理后,-0.15mm 石英砂岩颗粒粉末含Fe2O3 0.12% 和SiO2 99.42% 可达到含Fe2O3 0.01%,SiO2 99.8%,回收率在99%以上,达到光学玻璃用砂标准。
磁选
磁选工艺可以最大限度地清除包括连生体颗粒在内的赤铁矿、褐铁矿和黑云母等弱磁性杂质矿物。强磁选通常采用湿式强磁磁选机或高梯度磁选机。一般而言,对含杂以褐铁矿、赤铁矿、黑云母等弱磁性杂质矿物为主的石英砂,利用湿式强磁机在8.0×105 A/m 以上可以选出; 对含杂以磁铁矿为主的强磁性矿物,则采用弱磁机或中磁机进行选别效果比较好。上村宏、田渊平次采用强磁机对濑户石英砂进行了试验条件研究,结果表明,磁选次数和磁场强度对磁选除铁效果有重要影响,随磁选次数的增加,含铁量逐渐减少; 而一定的磁场强度下可除去大部分的铁质,但此后磁场强度即使提高很多,除铁率也无多大变化。另外,石英砂粒度越细,除铁效果越好,其原因是细粒石英砂中含铁杂质矿物量高的缘故。
浮选
浮选除去石英中的伴生矿物长石与云母最典型的工艺流程是以氢氟酸为活化剂,在强酸条件下 pH= 2-3采用胺类阳离子捕收剂进行浮选。但随着环保意识的增强,现在多采用无氟浮选法。例如: 在强酸( 一般为H2SO4) 性pH = 2-3 的条件下,用阴阳离子混合捕收剂优先浮选长石。这种工艺在内蒙古的通辽和新疆的昌吉已获得广泛应用。
美国硅砂选厂在酸性条件下,以石油磺酸钠和煤油为捕收剂,分离出黑云母及含铁矿物,使Fe2O3含量从0.12% -0.18%降至0.06% -0.065%。国外某选矿厂以高级脂肪胺盐和石油磺酸钠为捕收剂,亦获得了理想的分离效果。在高碱性介质条件下( pH=11-12) 以碱土金属离子为活化剂,以烷基磺酸盐为捕收剂,可优先浮选石英,实现石英与长石的分离,同时加入非离子表面活性剂,如1-十二烷醇,可使石英回收率急剧上升,而对长石影响不大,从而有利于二者分离。
常见的石英砂浮选流程可归纳为5 种,见图1。
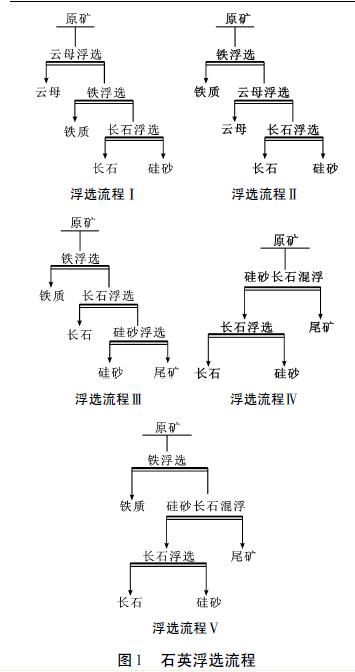
浮选流程1是最基本的流程,先用硫酸,将矿浆pH值调节至3 -4,用胺类捕收剂浮选云母,再用硫酸调节矿浆pH 值至4-5,用石油磺酸钠( ACCR-825)作捕收剂,浮选含铁矿物,最后用氢氟酸调节矿浆pH 值至2-3,用胺类捕收剂浮选长石,而硅砂作为尾矿回收。典型的有美国的Spruce pine 长石公司、国际矿物化学公司及Koerner 选矿厂。
浮选流程II是将浮选程I 中的云母浮选和铁矿物浮选顺序颠倒一下。选浮选流程III 先在矿浆pH 7-8 时,以脂肪酸作为捕收剂浮选含铁矿物,再添加氢氟酸和胺类捕收剂浮选长石,最后在矿浆pH 7-8 的条件下,用胺类捕收剂浮选硅砂,并作为泡沫回收硅砂精矿,这个流程对原矿中除含有铁矿物、长石、硅砂等外,并含有浮选前脱泥作业不能脱除的所谓杂砂时有效。浮选流程IV 是在矿浆pH 7-8 的条件下,用胺类捕收剂,将硅砂和长石的混合精矿作为泡沫回收,而将所谓的杂砂作为尾矿除去,再对混合精矿用氟氢酸和胺进行长石浮选,其泡沫为长石精矿,而尾矿为硅砂精矿。浮选流程Ⅴ是对铁含量比较高的原矿,预先脱铁再用浮选流程Ⅳ型进行浮选。
磁载体分选
作为一种新的细粒选矿方法,磁载体工艺近几年来引起了人们的广泛关注。该工艺的原理是,在混合悬浮物中磁铁矿颗粒选择性附着在一种矿物表面上,然后用磁选工艺除去被磁铁矿覆盖的矿物颗粒。影响磁铁矿颗粒附着的因素有矿物和磁铁矿的表面电荷,以及表面活性剂在这些矿物表面上的附着。通过控制这些参数可以分选许多种矿物。在这一工艺中,通常将强磁性相加入到非磁性或弱磁性悬浮液中。
V·波兹库尔特等利用磁载体分选工艺分离石英、钠长石和微斜长石,磁载体为磁铁矿。在有和没有十二烷胺存在的条件下,分别测试了石英、钠长石、微斜长石和磁铁矿的Zeta 电位。磁载体分选试验在由Zeta 电位测定结果所确定的条件下进行的。磁载体分选试验结果表明,石英和微斜长石在pH值为9.5 时可与钠长石分离,此时十二烷胺浓度为9.375×10-5 mol /L,加入的煤油量为2.1kg /t。在pH值为6 的条件下,石英和微斜长石也能达到一定程度的分离。同时还发现矿物表面的疏水性是比表面电荷更为重要的影响因素。
精提纯选矿工艺
一般而言,经过初提纯,石英砂中SiO2含量可达99.3% -99.9%。要获得更高的纯度,需进行精提纯。
酸浸
酸浸是利用石英不溶于酸( HF 除外) ,其他杂质矿物能被酸液溶解的特点,从而实现对石英的进一步提纯。酸浸常用酸类有硫酸、盐酸、硝酸、醋酸和氢氟酸。还原剂有亚硫酸及其盐类等。上述酸类对石英中的非金属杂质矿物均有较好的去除效果。
各种稀酸对Fe 和Al 的去除效果明显,而对Ti 和Cr的去除则主要利用较浓的硫酸、王水和氢氟酸处理。影响酸处理效果的主要因素是酸浓度、温度、时间、以及洗涤过程等。通常使用上述酸类组成的混合酸进行杂质矿物的酸浸脱除,考虑到HF 酸对石英的溶解作用,故HF 酸浓度一般不超过10%。酸浸各种因素的控制应根据石英最终品位要求,尽量降低酸的浓度、温度和用量,减少酸浸时间,以实现在较低的选矿成本下进行石英提纯。
根据酸浸温度不同,酸浸试验可分为热酸处理和冷酸处理。冷酸处理采用浸泡间歇搅拌浸出法,时间一般为24h。热酸处理一般时间较短,采用搅拌浸出。牛福生等的试验研究采用冷酸进行酸浸处理,只要处理时间长一些,是完全可以达到热酸处理效果的,其缺点是处理时间长,提高了石英砂的生产成本,优点是达到产品质量要求的前提下,最大可能地降低了酸气化而造成的环境污染。
包申旭等在制备高纯石英酸浸试验中,探讨了微波对提高酸浸效果、缩短反应时间所起的作用。在不用微波处理的条件下,室温下酸浸2h 后铁杂质的含量为0.0015%,用微波处理10min 后铁杂质含量即可下降到0.0013%,随着微波处理时间的延长,铁杂质的含量下降显著,微波处理时间到30min左右时铁杂质含量可以降到最低,达到0.0004% 左右,再延长微波时间则效果不明显。
微波利用材料在电磁场中的介质损耗而产生热量,由于石英和含铁杂质矿物具有不同的介电损耗因子从而造成在微波场中它们的升温速率各异,这就会在它们之间的界面上产生裂缝,从而促使石英中的包裹体的开裂,使含铁杂质矿物能被酸有效地去除。在微波场中进行酸浸试验,不仅可以促进含铁杂质矿物的去除,同时也可以大大加快反应速度,这对于提高生产效率、扩大生产规模具有重要的意义。
微生物浸出
用微生物浸出石英砂颗粒表面的薄膜铁或浸染铁,是最近发展起来的一种除铁技术。国外研究表明,用黑曲霉、青霉、假单胞菌、多黏菌素杆菌等微生物对石英表面薄膜铁浸除时,均取得了较好的效果,其中以黑曲霉菌浸除铁的效果最佳。Fe2O3的去除率多在75% 以上,精矿Fe203的品位低达0.007%。并且发现,用大多数细菌和霉菌预先培育的培养液浸除铁的效果会更好。目前,微生物除铁处于实验室研究阶段,规模化生产尚需进一步试验研究。
其他提纯方法
由于不同石英制品对杂质矿物含量的不同要求,有时也采用一些其他提纯方法作进一步提纯。如电选是利用石英与杂质矿物的电性上的微小差别,来选出微量金属杂质矿物; 热氯化方法,可除去石英中的气液相杂质和杂质矿物及金属包裹体等。
结语
( 1) 石英砂提纯方法及工艺流程由原砂中杂质矿物的赋存状态、选矿成本及精砂制品工业用途所确定。
( 2) 通过擦洗、磁选、浮选、酸浸等一系列工艺生产的高纯石英砂,已基本满足最终产品的质量要求。但在生产过程中要严防二次污染,如提纯水应采用去离子水,各种专业设备及工具尽可能不污染最终产品。
( 3) 制备高纯石英砂,重点是浮选和酸浸处理,特别是浮选药剂和酸浸时酸的选择; 随着环保意识的增强,无氟浮选工艺和药剂的研究是今后研究的重点。
( 4) 高纯石英砂作为大规模及超大规模集成电路、光纤、激光、航天、军事中的基础材料,其需求量越来越大,已经成为国民经济的战略性产品。结合化学、物理、微生物学、电磁( 波) 等专业知识,研究高纯石英砂的提纯技术是今后重要的发展方向。
|