硅微粉本身属于极性、亲水性的物质,与高分子聚合物基质的界面属性不同,相容性较差,在基料中往往难以分散,因此,通常需要对硅微粉进行表面改性,根据应用的需要有目的地改变硅微粉表面的物理化学性质。
为方便各位同行参考了解,粉体技术网特意整理了10个硅微粉表面改性配方,具体如下:
配方1:KH-550(环氧塑封料)
配方2:偶联剂Si-69
配方3:烷氧基硅烷低聚物
配方4:氨基、环氧基、乙烯基-苯基-氨基硅烷偶联剂(对比)
配方5:十六烷基三甲氧基硅烷、KH-560、KH-570(对比)
配方6:KH-550、KH-560、KH-570、A-171、甲基三甲氧基硅烷(对比)
配方7:KBM-573硅烷偶联剂、KH-550(对比)
配方8:Si-69、钛酸酯偶联剂(对比)
配方9:丙烯酸硅烷与硅氮烷复配
配方10:KH-560与N‑苯基‑γ‑氨丙基三甲氧基硅烷复配
配方1:KH-550(环氧塑封料)
改性剂:硅烷偶联剂γ-氨丙基三乙氧基硅烷(KH-550)
改性方法:(1)KH-550水解:改变水解溶液的种类、水解溶液不同的配比、水解溶液的pH值,通过对水解溶液电导率的监测,从而对硅微粉的水解程度进行评估。
(2)硅微粉改性:称取5g由蒸汽动能磨300℃蒸汽制得的硅微粉置于烧杯中,然后加入去离子水和乙醇的混合溶液,体积比为1:9。使用冰乙酸将溶液的pH调节至4左右,然后对固液混合物进行超声分散,使硅微粉与溶液充分混合,超声时间为15min,随后使用移液管加入不同质量分数的硅烷偶联剂,然后继续进行超声5min。将超声后的固液混合物使用恒温磁力搅拌器进行改性反应,温度设置为60℃反应时间为2h。将反应完成后的硅微粉进行抽滤、干燥,然后得到经过表面改性的硅微粉。
测试与表征:活化指数、吸油值、红外光谱。
改性效果:(1)用偶联剂、乙醇及去离子水的混合溶液对偶联剂进行水解最为有利,其中溶液的比例为V硅烷偶联剂:V乙醇:V水=1:1:9,水解溶液的pH=4。
(2)在硅烷偶联剂的添加量为4%、改性温度为100℃、改性时间为120min时,超细硅微粉的改性效果最好,其活化指数可以达到82.4%、吸油值为0.264mL/g。改性后硅微粉的红外光谱图中,有新的官能团的吸收峰出现,表明改性成功。
配方2:偶联剂Si-69
改性剂:偶联剂Si-69
改性方法:称取一定量不同粒度的硅微粉加入到水和乙醇混合溶液中,配置成45%的浆料,搅拌并升温,当体系温度达到110℃后,停止加热,加入一定量和相应比例的偶联剂Si-69,继续反应。反应结束后冷却,抽滤出料,干燥得到表面包覆改性的硅微粉。
测试与表征:接触角、FTIR、三元乙丙(EPDM)橡胶材料性能。
改性效果:(1)采用Si-69改性硅微粉,硅微粉的吸油值变小,活化率和界面接触角变大。当硅微粉的改性剂Si-69用量为1.5%时,其吸油值最小,活化率和界面接触角最大,说明改性效果最好。
(2)随着Si-69添加量的增加,EPDM复合胶料的ML先降低后增大,说明添加一定量Si-69的硅微粉其混炼胶的粘度下降,流动性提高,加工性能改善。且MH和MH-MLML呈增长趋势,说明Si-69改性硅微粉的加入会使得填料与橡胶之间形成的物理交联密度增多;焦烧时间t10稍有延长,正硫化t90时间明显延长。
(3)当Si-69改性硅微粉的添加量为1.5%时,EPDM复合胶料的硬度、拉伸强度、100%定伸强度和撕裂强度等综合性能最佳。
配方3:烷氧基硅烷低聚物
改性剂:乙烯基烷氧基硅烷低聚物(Vi-Psi)、氨基烷氧基硅烷低聚物(An-Psi)、多元烷氧基硅烷低聚物(X-Psi)
改性方法:将100g球形硅微粉放人电热恒温鼓风干燥箱于120℃干燥2h,冷却至室温。搅拌下将冷却后的硅微粉加人200g改性剂质量分数1.5%的乙醇溶液中,搅拌均匀后滴加0.8g蒸馏水,加热到100℃回流处理5h,冷却至室温,过滤、洗涤、干燥,即得经表面改性的球形硅微粉。
测试与表征:红外光谱、扫描电镜、粒度分布、环氧树脂力学性能。
改性效果:经表面处理后,硅微粉的粒径增大且尺寸均一性提高,硅微粉颗粒间夹杂碎片杂质的情况得到改善;添加改性硅微粉可提升环氧树脂的力学性能;在拉伸强度方面X-PSi改性硅微粉填充的环氢树脂拉伸强度提升幅度为8%,采用An-PSi改性硅微粉的环树脂则提升了6%。在断裂伸长率方面,采用An-PSi改性硅微粉的环氧树脂表现最佳,断裂伸长率增幅近60%。在弯曲强度方面,采用An-PSi和X-PSi改性硅微粉的环氧树脂弯曲强度增幅相近,均提升了12%左右。
配方4:氨基、环氧基、乙烯基-苯基-氨基硅烷偶联剂(对比)
改性剂:Z-6020(氨基硅烷偶联剂)、Z-6040(环氧基硅烷偶联剂)和Z-6032(乙烯基-苯基-氨基硅烷偶联剂)
改性方法:称取一定量的硅微粉在105℃条件下预热烘干1h,分别取3种类型偶联剂依次加入到5倍的醇水中(水醇体积比=9:1)配置成醇水混合液,控制溶液的pH值,搅拌15min。在一定温度下边搅拌边加入烘干后的硅微粉,持续搅拌30min后缓慢降至室温后置于105℃的真空烘箱中烘烤1h以上,然后碾碎过筛放入干燥器中待用。
测试与表征:接触角、TGA热失重分析、覆铜板性能。
改性效果:(1)接触角测试结果表明硅微粉经处理后改善了填料的表面特性使其呈亲油性。TGA热失重的结果表明偶联剂已完全包覆在无机硅微粉填料的表面,达到了改性的目的。
(2)使用环氧型Z-6040,用量为填料重量比例1%的偶联剂改性的硅微粉对覆铜板的耐热性改善效果最好。
配方5:十六烷基三甲氧基硅烷、KH-560、KH-570(对比)
改性剂:十六烷基三甲氧基硅烷、KH-560(γ-缩水甘油醚氧丙基三甲氧基硅烷)、KH-570(γ-甲基丙烯酰氧基丙基三甲氧基硅烷)
改性方法:将粒径3μm、20μm的硅微粉按照质量比1:4的比例进行复配,粉体含量65%,来探讨不同硅烷偶联剂对于导热灌封胶性能的影响。
测试与表征:导热灌封胶性能。
改性效果:在相同粉体添加量的情况下,十六烷基三甲氧基硅烷的性能要明显优于KH-560和KH-570,黏度最低,流平性最好,这是由于十二烷基三甲氧基硅烷为长链烷基,极性低,分子链段对于粉体表面的包裹性良好,而KH-560和KH-570分子链相对来说短一点,并且由于分别含有环氧基团和丙烯酰氧基,极性较大、分子间作用力强,进而造成黏度偏高,流平性偏低甚至有会一定程度的触变。因此,选用十六烷基三甲氧基硅烷作为粉体处理剂最为合适。
配方6:KH-550、KH-560、KH-570、A-171、甲基三甲氧基硅烷(对比)
改性剂:KH-550、KH-560、KH-570、A-171、甲基三甲氧基硅烷
改性方法:将100份硅微粉投入动力混合机中,升温至120℃搅拌干燥3h。将2份硅烷偶联剂均匀洒于粉体表面,在喷洒的同时进行搅拌。于120℃继续搅拌混合,并抽真空3h,即得改性硅微粉。
测试与表征:有机硅灌封胶性能。
改性效果:使用硅烷偶联剂对硅微粉进行改性后,灌封胶的黏度、沉降物平均质量显著降低,热导率略微下降,拉伸强度和拉断伸长率均有提高。其中,使用KH-550的灌封胶,力学性能和抗沉降效果均较好,拉伸强度为1.65Mpa,拉断伸长率为75%,沉降物平均质量仅为31g。
配方7:KBM-573硅烷偶联剂、KH-550(对比)
改性剂:KBM-573硅烷偶联剂、KH-550
改性方法:称取一定量的球形硅微粉放入真空干燥箱中,在120℃下干燥2h,取出后加入体积比为1:9的乙醇与纯水的混合溶液,超声分散30min,再逐滴加入一定质量分数的改性剂,将混合浆料置于恒温水浴锅中,在一定温度下反应一段时间。停止搅拌,取出放入真空干燥箱中,在80℃下干燥24h,得到表面改性的球形硅微粉。
测试与表征:红外光谱、SEM、吸油值、接触角和表面羟基数量,PTFE覆铜板性能。
改性效果:(1)耐热表面改性球形硅微粉的最佳制备工艺为:向球形硅微粉与纯水-乙醇混合液中加入质量分数为0.5%的KBM-573,在80℃的恒温水浴中高速搅拌反应1h。
(2)与未改性硅微粉相比,KBM-573硅烷偶联剂对球形硅微粉表面改性效果较好,团聚现象减少,分散性得到明显改善。
(3)与KH-550改性球形硅微粉相比,KBM-573改性球形硅微粉,具有更好的耐热性和应用性能。
配方8:Si-69、钛酸酯偶联剂(对比)
改性剂:Si-69、钛酸酯偶联剂
改性方法:偶联剂、去离子水和乙醇按体积比1:1:2混合,调pH=4,同时磁力搅拌12min,使偶联剂充分水解。然后将钛酸酯和Si-69分别按质量分数0.5%、1.0%、1.5%、2%的配比与干燥硅微粉混合,倒入球磨机,球磨30min。取出粉体干燥后继续球磨30min,烘干,得到改性硅微粉。
测试与表征:沉降时间、吸油值、活化指数、橡胶复合材料性能。
改性效果:(1)钛酸酯偶联剂和Si-69都可以改性硅微粉,提高了粉体的沉降时间、分散性和活化指数。其中钛酸酯和Si-69的用量为1.5%时对硅微粉的改性效果最佳。
(2)相比未改性的硅微粉,改性的硅微粉可提高天然橡胶的力学性能,并且分散性得到提高。拉伸强度、耐磨性和硬度相应都得到改善,采用1.5%用量的Si-69改性硅微粉,在天然橡胶添加量为20份时,复合材料的综合性能最佳,拉伸强度24.2MPa,磨耗体积0.48cm3,绍尔硬度50。
配方9:丙烯酸硅烷与硅氮烷复配
改性剂:丙烯酸硅烷KBM‑103,六甲基二硅氮烷、四甲基二硅氮烷。
改性方法:将石英砂或硅微粉、去离子水按比例混合,进行湿法研磨后,通过沉降或压滤,干燥、粉碎获得D50=1.0~20μm硅微粉原料;将硅微粉原料投入高速混合机中,加入丙烯酸硅烷偶联剂进行表面改性,改性温度为100~160℃,得到表面改性的硅微粉半成品;将表面改性的硅微粉半成品投入高速混合机中,加入硅氮烷进行二次改性,改性温度为40~110℃,改性结束后干燥去除残余的改性剂、氨气和水,得到表面改性硅微粉。
测试与表征:粒径、水分、羟基个数、乙烯基硅胶性能。
改性效果:湿法研磨得到一定粒度和羟基含量的硅微粉,该硅微粉的羟基能够和足够多的偶联剂进行反应,以便可以化学键合较多的硅烷偶联剂;然后选用含有双键且活性较强的丙烯酸硅烷偶联剂,使其参与聚合反应,改善产品强度;再选用硅氮烷对改性后的硅微粉进行二次改性,减少改性产品中残留的改性剂的羟基,解决产品放置过程中黏度变大、产品强度变差的问题;最后对二次改性后的硅微粉进行干燥处理,去除残留的改性剂、硅氮烷、氨气及少量水,提高产品的稳定性。所得活性硅微粉改性剂包覆量大,羟基含量少,改性剂残留少,稳定性好,应用于乙烯基硅胶中,随着存放时间的延长,乙烯基硅胶的黏度稳定,产品稳定性好,强度高,可用于导热硅胶、导热垫片、齿科印模材料等领域。
配方10:KH-560与N‑苯基‑γ‑氨丙基三甲氧基硅烷复配
改性剂:KH-560、N‑苯基‑γ‑氨丙基三甲氧基硅烷。
改性方法:采用硅烷偶联剂两步改性,即先采用经预水解的γ‑(2,3‑环氧丙氧)丙基三甲氧基硅烷在适当的温度下,经混合机干法改性,得到一次改性硅微粉;而后采用经预水解的N‑苯基‑γ‑氨丙基三甲氧基硅烷在适当的温度下,利用搅拌机湿法改性,得到二次改性硅微粉。
测试与表征:活化度、硅羟基含量、树脂混合物粘度。
改性效果:相比于未改性硅微粉、γ‑(2,3‑环氧丙氧)丙基三甲氧基硅烷改性的硅微粉、N‑苯基‑γ‑氨丙基三甲氧基硅烷改性的硅微粉,二次改性后硅微粉的活化度明显得到提升,硅微粉表面羟基数大大降低,硅微粉的疏水性得到增强。应用于环氧树脂时,树脂混合物的粘度大大降低,改善了硅微粉在环氧树脂中的分散性,提高了环氧树脂的加工性能。
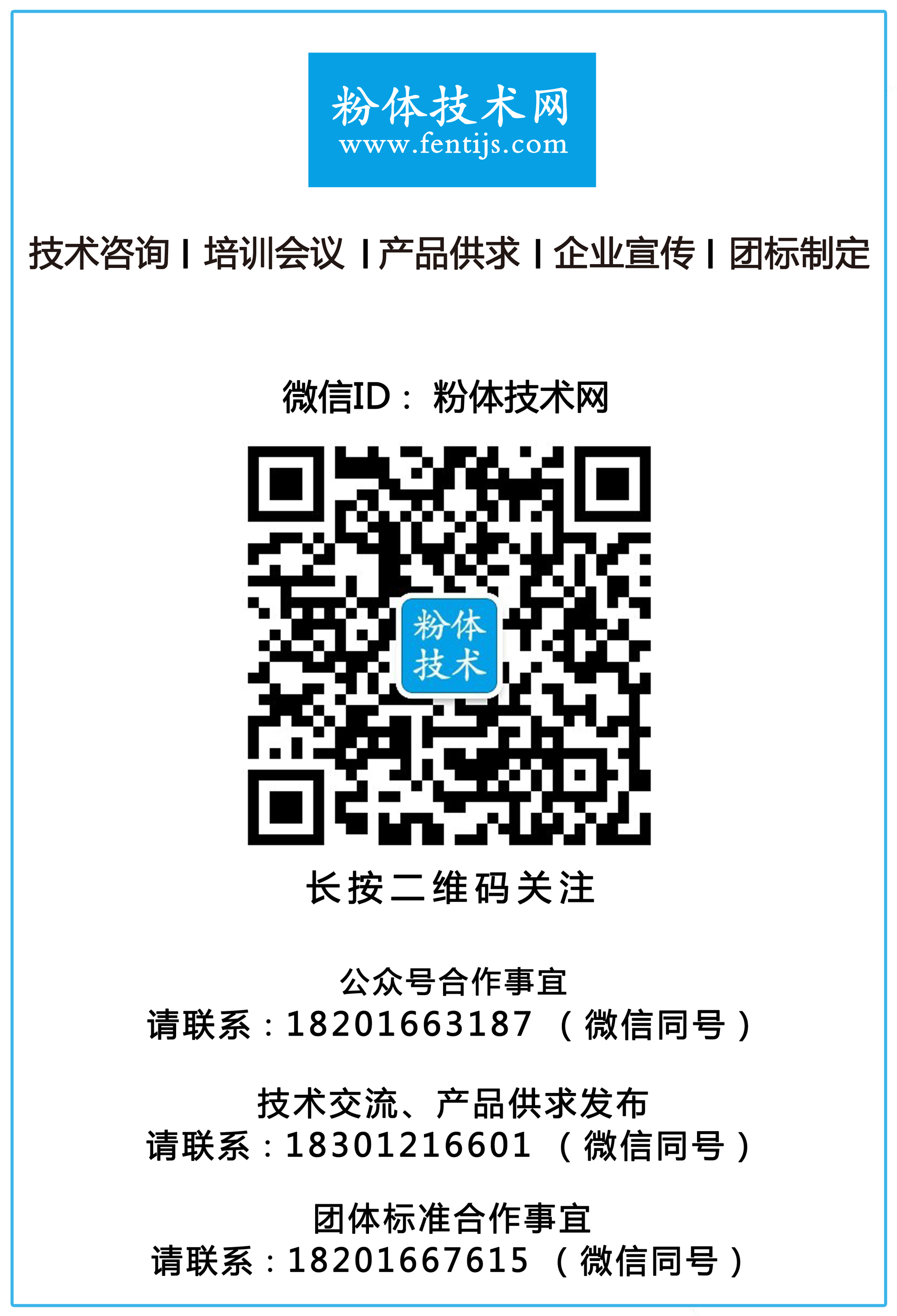
|