磷石膏是磷酸、磷肥产业的副产物。近年来,随着我国磷肥产业的迅猛发展,磷石膏的年堆存量不断增加,到2013年己经达到约7000万t,因此对磷石膏的资源化利用迫在眉睫。磷石膏多呈细粉状固体,颜色一般为浅灰或者黑灰色,其pH值偏低,一般介于1.5~4.5之间。磷石膏的主要杂质为磷和氟,除此之外还有少量的SiO2、Al2O3、Fe2O3、CaO、MgO及微量的重金属离子,少数地方的磷石膏还含有一些放射性元素。这些因素导致磷石膏的资源化利用率偏低,到2013年我国对磷石膏的利用率仅为27%。
磷石膏可在石膏行业、水泥行业、化工行业、农业等方面应用,其中,制备建筑石膏是合理资源化利用的途径之一,但在使用之前均需对其进行处理。本文主要针对湖北宜昌一化工厂的磷石膏进行了研究,分别探讨了锻烧温度、锻烧时间、粉磨时间及生石灰添加量对磷石膏制备建筑石膏性能的影响,并利用SEM、XRD、激光粒度分析等手 段对石膏的微观结构、形貌和物相等进行了分析,为规模化利用磷石膏生产建筑石膏提供了理论依据。
原料分析
磷石膏外观呈灰黑色,因含有较多的游离水,部分磷石膏呈现团聚状态;pH值为2.89,主要化学成分如表1所示,微观形貌分析如图1所示,XRD分析如图2所示。

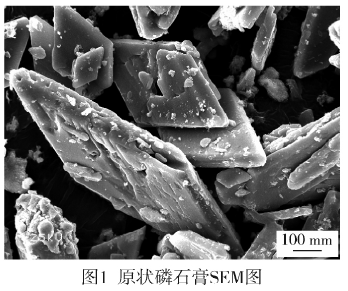
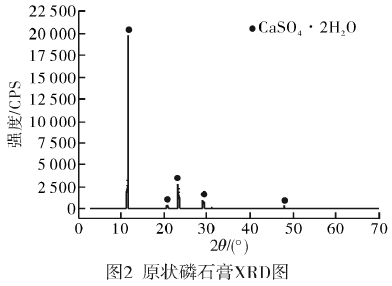
由图1可知,原状磷石膏主要以板状晶体存在,形状较为规则、均匀,但分布比较分散;晶体形状以菱形为主,也存在少量的三边形、五边形等。由图2可知,原状磷石膏的主要结晶相为二水硫酸钙。
实验方法
建筑石膏的制备:取磷石膏于瓷质托盘中,放入干燥箱45℃烘干。将干燥后的磷石膏和适量的生石灰于球磨机粉磨合适时间后放入瓷质托盘中,控制料厚约1 cm,选择在一定温度下锻烧,并保温适当时间。将锻烧好的石膏取出,自然冷却至室温,即为建筑石膏。
结果与分析
(1)锻烧温度对建筑石膏性能的影响
首先对原状磷石膏进行TG-DSC分析,结果如图3所示。由图3中TG(热重分析)曲线可知,该磷石膏样品在210℃左右失去18.66%的水分。从DSC(差动热分析)曲线可知,从大概70℃开始有不明显的吸热峰,说明在这个温度下磷石膏开始少量脱去水分。磷石膏第一次大量脱水从120℃左右开始,到150.09℃结束,说明二水石膏脱水放出的水蒸气分压达到一个大气压时的温度为150.09℃。从157.82℃开始,半水石膏开始脱水成AⅢ型无水石膏,到大约210℃结束。在620.08℃时,出现一个不太明显的吸热峰,此时,磷石膏脱水向Ⅱ型无水石膏转变。
根据上述分析,将锻烧温度的范围选定在130-170℃之间,每隔10℃设置一个梯度,保温时间为1.5 h,对磷石膏进行锻烧,经过一定时间的陈化后测试陈化前、后磷石膏的三相组成,见表2。
由表2可知,随着锻烧温度的增高,磷石膏三相中AⅢ型无水石膏的含量越来越高,HH半水石膏和DH二水石膏的含量越来越低,当温度为140℃时,得到的三相组成中半水石膏的含量较AⅢ型无水石膏的含量高,但二水石膏的含量高于5%,达不到纸面石膏板生产要求。当温度为150℃时,三相组成中二水石膏的含量为4.83%,低于要求的5%,但此时AⅢ型无水石膏的含量也有所上升,达到了44.82%,因此需要将样品放置陈化一段时间,使其中AⅢ型无水石膏吸收水分转变为半水石膏。当温度高于150℃时,AⅢ型无水石膏的含量会增多,此时会增加能源的浪费。经不同温度锻烧后的所有样品,在同样的条件下陈化后进行凝结时间和力学性能的测试,结果如表3和图4~图6所示。
由表3及图4可知,随着锻烧温度的不断升高,磷石膏的初、终凝时间都有所变化,呈现先降低后升高的趋势,其中在锻烧温度为150℃时,初凝时间为9 min,终凝时间为13min,同时,由图5和图6可知,在此温度下石膏的2h强度达到了最大值,抗折强度为1.90MPa,抗压强度为3.98 MPa。同时石膏的绝干强度分别为抗折强度2.8MPa和抗压强度4.83MPa,也出现峰值,与2h强度的变化规律一致。综合上述各个因素,当锻烧温度为150℃时,得到的建筑石膏的2h强度和绝干强度均最高,且锻烧温度较低,有利于节约能源,因此选定磷石膏制备建筑石膏的最佳锻烧温度为150℃。
(2)锻烧时间对建筑石膏性能的影响
磷石膏在锻烧过程中,锻烧时间过短,吸收的热量过少,不足以使二水石膏大量的脱水,造成石膏三相组成不均匀,胶凝性差;时间过长,会导致过多的半水石膏转化为AⅢ型无水石膏,不仅造成能源的浪费,还会影响石膏的性能。因此选取合适的锻烧时间极其重要。将锻烧温度确定为150℃ ,锻烧时间选定为1~2.5h,每隔0.5 h设置一个梯度,对150℃下锻烧不同时间的磷石膏样品进行与上述实验相同条件的陈化后对其进行力学性能测试,结果如表4和图7、图8所示。
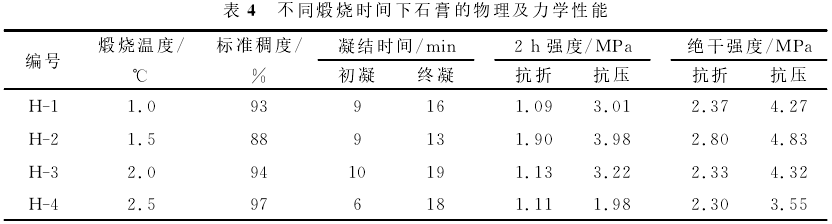
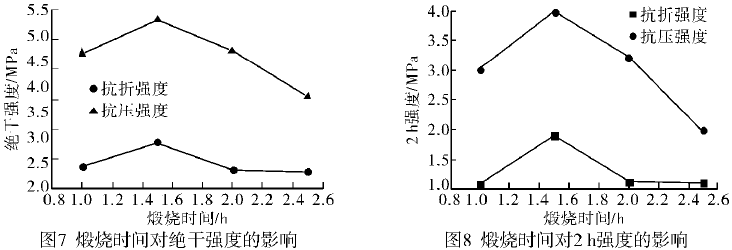
由图7、图8及表4可知,随着保温时间的不断延长,磷石膏的力学性能呈现先增长后下降的趋势,但变化幅度都不是很大,当锻烧时间为1.5 h时,石膏的2h强度达到了最大值,抗折强度和抗压强度分别为1.90 MPa和3.98 MPa,同时绝干强度也出现了峰值,抗折强度为2.80 MPa,抗压强度为4.83 MPa。标准稠度也呈现先增后减的趋势,变化幅度也不大,在保温1.5 h时达到最低值88%。因此,在150℃锻烧温度下,磷石膏的锻烧时间的选定为1.5 h较为合适。
(3)粉磨时间对建筑石膏性能的影响
由上述实验可知,虽然通过优化锻烧工艺可以改善产品——建筑石膏的部分性能,但其标准稠度仍然偏大。石膏标准稠度偏大的原因是因为其板状的晶体结构,这种结晶类型导致其作为胶凝材料时流动性比较差,需水量大。因此,对原状磷石膏进行粉磨,有利于减小晶体尺寸,获得晶体尺寸较小的建筑石膏,同时石膏的流动性有所增加并且需水量降低。球磨是一种有效的粉磨工艺手段,球磨时间的长短对磷石膏的性能有着极大的影响。实验采用SM-500型球磨机,球磨时间分别设定为1 min、2 min、3 min、4 min、5 min及6 min。取不同球磨时间的样品进行测试,结果见表5。
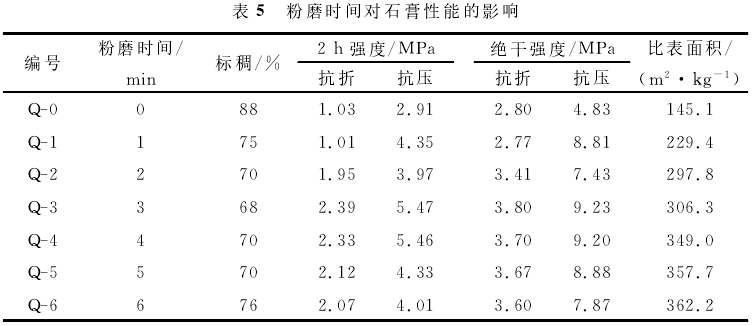
由表5和图9可知,随着球磨时间的不断延长,磷石膏的比表面积不断的增大,即磷石膏的颗粒越来越细。从图9曲线中可以看出,球磨时间从0 min增加到2 min的过程中,比表面积增长迅速,从2 min增加到4 min时,比表面积的增长变缓,而从4 min以后,再增加球磨时间,比表面积几乎不再增长,而是趋于一个稳定的值。这是因为固体物料的粉碎首先主要依靠物理碰撞、研磨而导致颗粒变小、比表面积增大。但在颗粒逐渐细化的过程中,物料所在空间有限,得不到充分的分散,颗粒又会在同一研磨介质(钢球)作用下,促使颗粒团聚或包裹其研磨介质,导致研磨效率降低。因此,可以认为粉碎到一定程度时,会出现“粉碎一团聚”现象,即粉碎和团聚可逆。当这两个过程速度一致时,颗粒尺寸达到极限值,此时机械力不足以抗衡物料颗粒更高的断裂强度,只能维持物料颗粒粒度平衡,此时再增长球磨时间只是徒劳。
由表5、图10及图11可知,随着球磨时间的增长,石膏的力学性能先增强后减弱。在球磨之前,其2h抗折强度为1.03 MPa,抗压强度为2.91 MPa,绝干抗折强度为2.80 MPa,抗压强度为4.83 MPa;当球磨时间增长到3 min时,其2 h抗折强度为2.39 MPa,抗压强度为5.47 MPa。同时绝干抗折强度达到了3.80 MPa,抗压强度达9.23 MPa,较球磨前分别提高了35%和91%,提高幅度较大。而当球磨时间大于3 min时,随着球磨时间的增长,2h强度和绝干强度均有所下降,但是下降幅度较小。这是因为颗粒粒度对石膏的水化有着一定的影响。颗粒粒度较小,石膏表面与水的接触面积比较大,因而溶解速率比较快,有利于石膏晶体成核,提高了硬化体的强度;但是当球磨时间过长时,石膏颗粒粒度过小,颗粒在液体中发生团聚,难于分散,因而导致石膏硬化体产生较大的结晶应力,石膏硬化体缺陷增加,引起力学强度的下降。
同时,从表5中得知,当颗粒粒度减小时标准稠度随之下降,这是因为球磨破坏了石膏比较均匀的板状形貌,增大了与水的接触面积,增加了其流动性,因此适当的球磨会降低石膏的标准稠度。但是随着球磨时间的增加,标准稠度又有所上升,这是因为颗粒过细时,在与水接触时团聚程度会增加,引起标准稠度的增加。为了进一步探究球磨对石膏性能的影响,对球磨后的样品进行激光粒度分析,结果如图12所示。
由图12(a)可知,球磨前原状磷石膏的粒径分布范围比较窄,平均粒径为42.2μm,颗粒分布带窄,小于10μm的颗粒比较少。胶凝材料的颗粒级配是影响其性能的主要因素,因此对磷石膏进行球磨以改变其颗粒级配是非常有必要的。从图12(b)中可知,当使用球磨机对磷石膏球磨3 min后,其平均粒径为25.5 μm,颗粒分布带变宽,小于10μm的颗粒大幅增加,各个粒径所占的比例也更加均匀。由图12(c)可知,当球磨时间继续增长之后,小于10 μm的颗粒数量小幅增加,峰宽变化不大,其颗粒平均粒径为23.2μm,较球磨3 min时略有下降。由此可见,3 min之后再增加球磨时间,石膏的平均粒径己经不会再大幅度减小了,也间接说明了球磨效率下降,即出现“逆粉磨”现象,从而导致锻烧后磷石膏(即建筑石膏)的力学性能也有所下降。
(4)生石灰对建筑石膏性能的影响
经过上述锻烧制度及球磨的处理,制得的建筑石膏性能得到了较好的改善,但是其pH值仍为2.87,呈较强的酸性,而在一些应用领域,需控制石膏体系的pH为4~7,如生产纸面石膏板。实验中利用生石灰对磷石膏进行改性处理,将生石灰与磷石膏按照比例称取后放入球磨机,球磨3 min后取出,在150℃下锻烧1.5 h并陈化后得到建筑石膏,测试建筑石膏的力学性能,如表6所示。
从表6中可以看出,随着生石灰添加量的增多,建筑石膏的pH值不断增加,当生石灰添加0.7%时,建筑石膏的pH值为6.13,接近中性。随着生石灰的添加,建筑石膏呈碱性,同时,建筑石膏的强度也呈先增后降的趋势,在生石灰添加量为0.4%时,试样抗折强度和抗压强度均达到顶峰,抗折强度为5.93 MPa,抗压强度为11.50 MPa。
利用改性后的石膏制备标准石膏试块,尺寸为40 mm X 40 mm X 160 mm,对其微观形貌进行分析,如图13、图14所示。
由图13、图14可知,在未掺加生石灰时,体系中存在的酸性物质阻碍了半水石膏中晶体接触点的形成,使晶体大多数按照一定的方向排列,相互之间基本无交错现象,晶体的形状多为柱状及针状,也存在少数板状。放大至5 000倍时更能进一步地看到部分晶体之间只是松散地搭接在一起,且大部分的晶体按照一个方向堆积,并未形成很紧密的交叉结构,这些都对石膏试块的宏观强度有不利影响。当掺加0.4%的生石灰对建筑石膏进行改性后,生石灰将体系中的酸性物质转化成惰性物如磷酸钙等,从而减弱了酸性物质的阻碍作用,使得石膏中的晶体接触点变多。由图14可知,晶体之间不再是同向排列,而是纵横交错,相互交叉在一起。放大至5 000倍后可以更明显地看到晶体之间相互交叉联生,搭接的密实程度也有所增加,结晶接触点变多,在宏观上呈现为试块的强度得到增强。
(5)建筑石膏性能
经过上述实验后可知,该磷石膏制备建筑石膏的最佳制备配比及工艺为:将0.4%的生石灰与磷石膏一起球磨3 min后,在150℃下锻烧1.5 h后陈化一定时间。将得到的建筑石膏的性能与标准GB/T 9776-2008《建筑石膏》中的优等品技术指标要求进行对比,结果见表7。
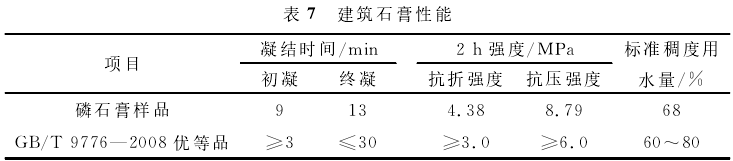
由表7可知,经过一系列处理的磷石膏制备的建筑石膏各项性能都达到了GB/T9776-2008《建筑石膏》中优等品技术指标的要求。
结论
(1)随着锻烧温度的升高及锻烧时间的延长,由磷石膏制得的建筑石膏力学性能出现先增后降的趋势,在150℃条件下锻烧1.5 h得到的建筑石膏性能最好,2h抗折和抗压强度分别为1.90 MPa和3.98 MPa,绝干抗折强度为2.80 MPa,抗压强度为4.83 MPa,初凝时间为9 min,终凝时间为13 min。
(2)对原状磷石膏进行粉磨,可以大幅降低建筑石膏的标准稠度需水量,明显提高其力学性能。当粉磨时间为3 min,磷石膏比表面积为306.3 m2/kg,经锻烧制得的建筑石膏标准稠度为68%,2 h抗折和抗压强度分别为2.39 MPa和5.47 MPa时,绝干抗折和抗压强度分别可达到3.80 MPa和9.23 MPa。
(3)利用生石灰对磷石膏进行改性,石膏晶体中结晶接触点增多,宏观力学强度提高。当生石灰添加量为0. 4%时,制得的建筑石膏的性能最佳,2h抗折强度为3.38 MPa, 2 h抗压强度为6.79 MPa,达到了GB/T 9776-2008《建筑石膏》中优等品的技术指标要求。
作者:李箫等
更多精彩!欢迎扫描下方二维码关注中国粉体技术网官方微信(粉体技术网)
|