|
|
液相法合成高纯石英粉的研究进展 |
来源:中国粉体技术网 更新时间:2014-12-10 10:19:48 浏览次数: |
|
|
与气相合成法相比,液相合成法具有反应温度低、设备简单,能耗少等优点,目前工业上广泛采用液相合成法制备超微粉。在液相中合成超微粉,能精确控制组分含量;能实现分子/原子水平的均匀混合;有溶剂稀释,易于控制反应;便于添加其他组分,制备掺杂型氧化物粉体。目前,用于制备石英粉体的液相合成法主要有溶胶-凝胶法、沉淀法、微乳液法、液相水解法等。
1.1 溶胶-凝胶法(Sol-Gel)
1968 年,Stöber 等系统地研究了硅酸酯-醇-水-氨水体系合成SiO2 微粒。由于该工艺制备得到的SiO2 粒子具有尺寸和形状的均一性好、尺寸可控、组成单一和表面易功能化等特点,迄今仍被广泛采用,被称之为Stöber 工艺。
赵丽等通过透射电镜(TEM)重点研究了该体系中各种反应条件如溶剂类型、各组分(氨、水、TEOS 等)浓度、水解温度等对SiO2 颗粒大小和形貌的影响,并制备得到了粒度可控的单分散SiO2 球形颗粒。
Rao、申晓毅和颜培力等研究利用超声波工艺在TEOS-醇-水-氨体系中制备超微SiO2 粉体。利用超声空化作用产生的高能冲击波和微射流的共同作用,不仅提高了水解和缩聚反应的速率,而且一定程度上防止了SiO2 颗粒的团聚,使凝胶颗粒粒度可控、介观分散均匀、分布窄。
李德慧等在醇类有机溶剂中,以氨水为催化剂,TEOS 在分散剂作用下水解,经真空低温冷冻干燥制得了单分散、球形实心、粒度分布窄的高纯SiO2 颗粒。真空低温冷冻干燥,使SiO2 水悬浮液中冻结的水分在低温低压下升华而脱去,最大限度地避免了干燥过程中SiO2 粒子的团聚,从而得到单分散的SiO2 粉体。
此外研究表明,在酸性体系中也可以利用硅醇盐水解制备SiO2 微粒。Kawaguch和 Karmakar等分别利用正硅酸乙酯(TEOS)-硝酸-水和正硅酸乙酯(TEOS)-醋酸-水体系制得了致密的SiO2 微粒。
Karmakar 等研究了含有机或无机酸-水-TEOS 的体系,结果表明,在pH 值为 l.35~2.25 的条件 下,即可制得致密的SiO2 微粒。
Yang利用TEOS-HNO3-水-乙醇体系制备SiO2 溶胶,研究了反应物的配比和反应温度对SiO2 溶胶粒径的影响及SiO2 溶胶在陈化过程中的稳定性。
比较发现,在碱性体系下水解速率较慢,但缩合速率较快,主要形成较大的SiO2 微粒;在酸性条件下水解速率较快,但缩合速率较慢,而反应所产生的微粒则是以小颗粒居多而成串长大。
溶胶-凝胶技术制备石英粉体有许多优点:
①由于所用原材料是化学反应剂,可以精制成不带任何金属杂质,而且消除了杂质的其他来源;
②容易调节羟基含量和掺杂;
③由于所有操作过程均在较低温度下进行,制造成本较低;
④可以通过控制反应条件选择合成一定粒径范围内的高度单分散SiO2 球形颗粒。
但是到目前为止,此项工艺技术仍存在一些问题,主要是:
①用溶胶凝胶法制备SiO2 粉残余碳不易完全清除的问题,使其产生黑斑,影响纯度和外观质量;②由于反应得到的颗粒细小,表面能高而易团聚,导致形成的SiO2 颗粒存在残留小孔洞;
③原料主要是有机硅烷,不仅原料成本较高,而且有机溶剂对人体有一定的危害性;④反应时间较长,不利于工业化规模生产。因此,此法在原料的广泛性上需进一步研究,以降低工艺成本,提高此方法的适用性。同时,如何改变工艺控制(如水解体系、干燥方式及烧结途径等)以缩短生产周期等仍是将来有待解决的难题。
1.2 化学沉淀法
沉淀法是液相化学合成石英粉体较为广泛的方法之一。它是以水玻璃(Na2SiO3)和盐酸或其他酸化剂为原料,适时加入表面活性剂到反应体系中,控制合成温度,直至沉淀溶液的pH 值为8 左右加入稳定剂,将得到的沉淀用离心法分离洗涤,经低温干燥,最后高温灼烧一定时间后得到石英粉体。
该方法原料易得,生产流程简单,能耗低,投资少。沉淀法根据使用的酸又分为盐酸沉淀法和硫酸沉淀法。硫酸沉淀法操作条件稳定,它较气相法投资少、设备简单,成本低;较盐酸沉淀法原料成本低,工艺简单。
利用水玻璃和酸反应制备石英粉体的机理以及SiO2 粉体的粒度、形貌与分散性控制方面,许多研究人员进行了大量的实验与探索。
李清海等利用水玻璃与甘油混合溶液和硫酸溶液在高速搅拌下制备了球形SiO2 颗粒,并通过 SEM、XRD 和TGA研究了沉淀法与研磨法制备SiO2 微粉的区别。研究表明:沉淀法获得的SiO2 粉体为无定形态,粒度小且呈球形,而球磨法获得的SiO2 粉粒度相对较大,颗粒为非球形且不均匀;合成的SiO2 粉体颗粒Si-OH 键在500~600 ℃发生羟基缩合脱水反应,而且SiO2 粉在1384.71 ℃时开始出现玻璃态。
Sheng 等通过控制沉淀反应时间与溶液pH 值、温度、溶液浓度等,制得了呈球形的SiO2 颗粒,平均粒径为425 nm。而Ja和Jesionowski等以工业水玻璃和盐酸为基本原料,采用化学沉淀法制备SiO2颗粒,其制得的SiO2 颗粒形貌为非球形颗粒。
近几年以沉淀法为基础派生了多种制备方法,如何清玉和刘海弟等将沉淀过程置于超重力反应器,在超重力环境中强化微观混合和传质过程,缩短反应时间,制得的SiO2 颗粒粒径小、粒度分布窄。
Jesionowski 等利用碳化反应法制备了SiO2 粉体,即采用水玻璃与CO2 进行反应生成含水的SiO2固体颗粒沉淀,经干燥、烧结、研磨、过筛等过程,得到石英粉体。
虽然沉淀法制备石英粉体具有诸多优点,但是其缺点也不容忽视:①工业级水玻璃的杂质含量太高,很难获得较高纯度的SiO2 粉体;②反应体系的浓度较低,沉淀速度快,沉淀过程不易控制;③沉淀法制备的SiO2 粉体颗粒表面含有大量的羟基,使SiO2 原生粒子之间形成氢键的机会大大增强,造成严重的团聚现象,在电子显微镜下可观察到非常大的SiO2 聚集体,降低了粉体的使用率和消弱了产品的结合力,补强性能也较差。
采用沉淀法获得的SiO2 粉体表面羟基含量是同级别的气相法制备得到的SiO2 粉体颗粒的三倍以上。正因如此,采用沉淀法生产的SiO2 粉体的原生粒子的平均直径一般是无法给出的,而是给出SiO2不变聚体的平均直径,因为该直径能更好地表达与补强作用的关联性。
1.3 微乳液法
在反相微乳液介质中合成 SiO2 时,一般用烷基硅酸酯(如TEOS)或工业水玻璃(主要成分Na2SiO3)为硅源,酸或碱溶液(包括HCl、HNO3 或氨水、NaOH溶液)为分散相。它们不但作为催化剂,而且其中的水还可作为反应剂。用烷基硅酸酯为硅源时,酸、碱都可作为催化剂,把烷基硅酸酯加到含有催化剂的反相微乳液中,其分子就从油相通过表面活性剂界面层渗透到反胶束液滴中,发生水解和缩合反应,这属于单微乳液法。
当Na2SiO3 为硅源时,一般用酸作催化剂,将分别含Na2SiO3 和酸的两种组成相同的反相微乳液混合发生反应,这属双微乳液法。
何晓晓等利用 TritonX-100/环已烷/正已醇/水反相微乳液体系制备了单分散及粒度可控的SiO2 颗粒。
骆锋等以硅酸盐溶液/环己烷/聚乙二醇辛基苯基醚/正戊醇体系的微乳液反应为基础,以浓硫酸为沉淀剂,并采用共沸蒸馏脱水工艺制备了粒径为15~35 nm,比表面积达580~630 m2/g,近似球形的非晶态SiO2 颗粒。共沸蒸馏工艺能充分地脱去凝胶中残余的水分,防止因含水胶体干燥过程引起的粉末硬团聚,从而显著地提高了粉体的性能。
沈风雷等利用拟三元相图研究了不同表面活性剂/助表面活性剂比、水相变化对微乳液形成的影响,并得到了稳定的油包水型微乳液。对含硅酸钠的微乳液酸化后可制备得到SiO2 颗粒,其粒径约为30nm,晶型为β-石英。
微乳液法制备石英粉体具有实验装置简单,能耗低;所得颗粒粒径分布窄,且单分散性、界面性和稳定性好。但是由于其成本高、产品的有机成分难于去除且易造成环境污染,而尚未在工业上广泛应用。为了实现工业化生产,在工艺上尚需进一步研究,实现有机组分的分离与回收,以及寻求有效的途径实现去除产品有机杂质的同时防止颗粒的团聚等。
1.4 液相水解法
液相水解法制备石英粉体系指利用 SiCl4 与纯水发生水解和缩聚反应,再将水解产物经洗涤、液固分离、干燥、锻烧、研磨和筛分等工序,制备SiO2粉体的方法。
Zhao 等采用SiCl4 的液相水解法制备得到了结晶形态为方石英,非球形的石英粉体,并利用该合成粉体在氢-氧火焰中制备了高纯低羟基石英玻璃。
魏昭荣等通过严格控制SiCl4 的水解温度和水解加水量来有效控制水解反应的过程,但由于SiCl4的液相水解反应放出大量的热,要控制水解温度很困难,根据能量守恒原理,需要消耗大量的能量来维持温度的恒定,这样成本高导致产品价格高,工业化很难实现。
Shunichiro 等在SiCl4 液相水解过程外加了高速搅拌装置(300 r/min),以达到反应均
匀和促进散热等,制备了高纯低羟基石英粉体。
Hiromichi 等利用饱和盐酸代替纯水与SiCl4 发生水解反应,在这种情况下的水解产物为悬浮物而不是胶体,易固液分离,产生的盐酸在溶液中不溶解而是直接挥发,在保持酸性不变的条件下继续进行水解反应,经干燥、高温煅烧后得到的高纯石英粉。
张香兰等则采用SiCl4 与碱液反应制备了石英粉体。研究表明,氨水和Na2CO3 浓度增大引起的粒径变化比NaOH 浓度增大引起的粒径变化小。利用SiCl4 与碱液反应制备高纯SiO2 粉能耗小、成本低,工艺控制简单,正硅酸沉淀与体系溶液分离容易。SiCl4 液相水解法制备石英粉,不仅原料低廉易得,而且不含碳,可以制备得到高纯度低羟基的SiO2粉体。但是,工业化生产过程SiCl4 与水反应剧烈,水解过程难以控制,粉体易团聚,很难形成致密的石英粉。因此,为了实现工业化,此法在工艺控制(如水解控制、干燥及烧结过程等)有待进一步研究,以有效防止颗粒的团聚等。
1.5 展望
综上所述,气相合成法制备石英粉纯度高,反应速度快,生产条件易控制,适合大规模生产,但是成本高,设备复杂且要求高;液相法制备石英粉的方法能耗少、成本低,设备简单,但是共同的缺点是粉体易团聚,制备周期长,不利于工业化生产。利用SiCl4 为原料,采用气相法或液相水解法制备高纯合成石英粉的发展潜力巨大。
目前我国拥有年产10 万吨的多晶硅产能,而每生产1 吨多晶硅就副产10~15 吨SiCl4,而SiCl4是高毒性物质,处理不当会对环境产生巨大污染。因此,利用SiCl4 制备高纯合成石英粉,既能基本解决多晶硅副产物SiCl4 的环境污染问题,化害为利,又能节约水晶资源,实现变废为宝,符合高效循环经济的发展,从而获得巨大的经济效益和社会效益。
但气相法因其制备成本高、设备要求高、技术复杂,要进一步降低产品成本很困难。而SiCl4 液相水解法则具有成本上的独特优势,综合其他各种化学合成法的优点,不断改进深入研究,一旦在水解反应过程的有效控制、粉体团聚等关键技术方面有所突破必将成为制备高纯石英粉的首选技术。如利用气-液反应法的有效结合达到控制SiCl4 液相水解反应的过程;利用液相合成法常用的超声分散技术、冷冻干燥技术、超临界干燥技术、添加剂分散技术等方法,使水解反应和干燥烧结等过程得到控制,从而防止颗粒团聚,使石英粉体性能得到改善。
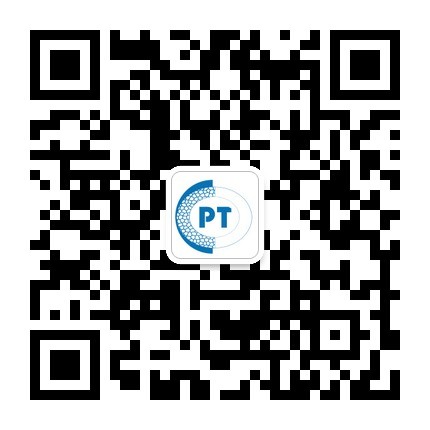
|
|
|
|
|
|
|
|
|
|
|
|