|
|
15种功能粉体表面改性配方汇总 |
来源:中国粉体技术网 更新时间:2025-04-14 09:26:15 浏览次数: |
|
|
粉体的表面改性在很大程度上是通过表面改性剂在粉体表面的作用来实现的。因此,表面改性剂的配方(品种、用量和用法)对粉体表面的改性效果和改性后产品的应用性能有重要影响。表面改性剂的配方包括选择品种、确定用量和用法等内容。
为此,粉体技术网特意搜集整理了纳米氧化锌、氢氧化铝、氢氧化镁、硫酸钙晶须、活性硅酸钙、氧化铁黄颜料、勃姆石、云母钛珠光颜料、片状锌粉、超细碳化硅粉体、三聚磷酸铝防锈颜料、铝粉、白炭黑、电气石粉、导热填料氧化铝等15种功能粉体表面改性剂配方,具体如下:
改性方法:取适量纳米ZnO放在真空干燥箱中预干燥,无水乙醇和去离子依照质量比3∶5混合,在干燥后的烧杯中加入纳米ZnO和上述溶液.超声破碎处理30min,在1000r/min下,搅拌1h,匀速搅拌后待温度恒定,缓慢匀速滴加硅烷偶联剂(溶于无水乙醇),反应结束后冷却至室温,溶液用无水乙醇清洗3次、离心机离心3次,然后置于真空干燥箱干燥,制得偶联剂改性后纳米ZnO。
改性剂:硅烷偶联剂(KH-570),最佳用量3%,反应时间2h,反应温度60℃。
测试与表征:活化指数、傅里叶变换红外光谱表征、扫描电镜表征、X射线表征。
改性效果:纳米ZnO表面由亲水性变为疏水性,纳米粒子的团聚现象改善,分散稳定性提高。FT-IR分析表明,硅烷偶联剂KH-570成功改性纳米ZnO粉体;XRD衍射和SEM分析表明,是否改性并不会改变纳米ZnO粉体的六方晶型结构,但纳米ZnO粉体团聚现象显著改善。
改性方法:氢氧化铝粉体于120℃下干燥6~8h,加入石油醚溶剂制成浆料,装入三口烧瓶置于搅拌器之上,打开搅拌器,用滴管缓慢加入事先调配好的改性剂,高速搅拌反应约30min,真空抽滤样品,烘干,打散制成粉末状。
改性剂:钛酸酯偶联剂,最佳用量0.5%,最佳改性温度110~120℃。
改性效果:氢氧化铝予以表面改性处理后,在硅橡胶涂料中分散就较为均匀了,团聚现象虽然仍然有,但是已经得到了大大改善,并较大程度地提高了复合材料的相容性以及电气绝缘性。
改性方法:在恒温80℃条件下,将分散在无水乙醇中的改性剂(2%)溶液与氢氧化镁按1∶1.5的比例配成浆料,改性2h。改性完抽滤、135℃烘干、研磨得到改性氢氧化镁粉末。
改性剂:钛酸酯偶联剂CS-201、CS-311,含磷有机阻燃剂磷酸甲酚二苯酯、亚磷酸二甲酯,用量2%,改性2h。
测试与表征:红外光谱、热重、电镜和粒度,并将将制得的改性氢氧化镁作为阻燃剂加入EVA中测试材料性能。
改性效果:钛酸酯偶联剂CS-201、CS-311和有机阻燃剂磷酸甲酚二苯酯、亚磷酸二甲酯改性MH都能起到降低颗粒团聚的作用,提高粒径的分散性,效果最好的是钛酸酯偶联剂CS-311。有机阻燃剂磷酸甲酚二苯酯改性MH,能提高氢氧化镁耐热性和高温下质量保持率。钛酸酯偶联剂CS-311改性后的氢氧化镁与EVA树脂的相容性最好,极大提高断裂伸长率;磷酸甲酚二苯酯改性改性后的氢氧化镁阻燃效果最好。
改性方法:首先按照比例称取绝干质量为10g的硫酸钙晶须和一定量的氯化镁(相对于硫酸钙晶须绝干质量的10%,20%,30%)分别置于250mL烧瓶和100mL烧杯中待用;然后量取一定量的磷酸溶液(磷酸与氯化镁的摩尔比为1∶1),用去离子水稀释至200g后置于水浴锅中(水浴温度为25℃),再用氨水调节磷酸溶液pH值并将其缓慢倒入装有晶须的烧瓶中;将烧瓶置于一定温度和转速的磁力搅拌器中;最后将称量好的氯化镁溶于20mL的去离子水中,待其完全溶解后转移至恒压漏斗中并缓慢滴入烧瓶中;反应完成后,经过滤、洗涤和烘干得到改性硫酸钙晶须。
改性剂:氯化镁用量(相对于硫酸钙的绝干质量)为30%,改性温度为60℃,改性pH为9.0,改性时间为20min。
测试与表征:溶解度、粒径和表面形态、热重、白度,手抄片抄造和性能检测。
改性效果:改性后硫酸钙晶须在水中的溶解度可由0.25wt.%降低至0.02wt.%,当加填量为30%时,留着率可由24.5%提升至78.4%。将晶须改性后加填,可在一定程度上提高纸页的白度、不透明度。当纸页中填料含量介于5%~25%时,改性晶须的加填效果比传统造纸填料(碳酸钙和滑石粉)的加填效果更好。
改性方法:将工业制备的活性硅酸钙粉体和硬脂酸同时加入蒸压反应釜,温度120℃,搅拌速率500r/min,恒温时间30min,反应结束后使用自来水快速冷却反应釜,将粉体取出后充分沉淀,过滤后在鼓风干燥箱中100℃下烘干。
测试与表征:吸油值、红外光谱、扫描电镜和热重分析,并将改性后的粉体加入到硅橡胶中制成复合材料测试性能。
改性效果:随着硬脂酸用量增加,吸油值不断降低;硬脂酸和粉体间存在化学吸附;添加1%硬脂酸可以使硅橡胶拉伸强度比未改性粉体增加40%。硬脂酸用量从1%增加至8%,拉伸强度降低,扯断伸长率先增加后降低,硬脂酸用量为4%时,扯断伸长率达到最大,硬脂酸用量为8%时,拉伸强度和扯断伸长率最低。
改性剂:以硅烷偶联剂γ-甲基丙烯酰氧基丙基三甲氧基硅烷(KH-570),十六烷基三甲基溴化铵(CTAB)。
改性方法:取120g白炭黑加入到2L四口烧瓶中,加入600g去离子水、一定量的CTAB,以250r/min搅拌并升温至65℃,调节pH至一定值,接着再加入体积比为1:1的乙醇和KH-570混合液,在一定温度下改性1.5h。将产物过滤、洗涤后,105℃烘干得到改性白炭黑。
测试与表征:黑活化度、表面羟基数、XRD、FT-IR、TEM,将改性白炭黑用于丁苯橡胶补强测试材料性能。
改性效果:CTAB质量分数为4%,KH-570质量分数为10%,反应温度为65℃,反应时间为1.5h,pH为6,改性后的白炭黑表面羟基数最少,为2.02个/nm2,活化度达100%。改性白炭黑用于丁苯橡胶进行应用研究表明,改性白炭黑能降低橡胶的门尼黏度、硫化时间,改善加工性能。橡胶的定伸应力以及断裂伸长率等力学指标有效改善,体积磨耗下降,提高橡胶耐磨性能。
改性剂:γ-甲基丙烯酰氧基丙基三甲氧基硅烷(KH-570)、双-(γ-三乙氧基硅基丙基)四硫化物(Si-69)、异丙基二硬脂酰氧基铝酸酯(Al-60)。
改性方法:采用湿法改性,将改性剂和无水乙醇按质量比10:1混合搅拌均匀后装入分液漏斗。将电气石粉和去离子水放入三口烧瓶,超声分散10min后置于90℃油浴锅中,以1000r/min转速机械搅拌,同时通过分液漏斗加入改性剂/无水乙醇分散液。分散液于15min加入完毕.继续反应2h,抽滤,洗涤,干燥,即得改性电气石粉。其中,电气石粉与改性剂的质量比为100:10。
测试与表征:通过机械共混法制备天然橡胶/电气石粉复合材料,测试其硫化性能、物理机械性能、动态力学性能等。
改性效果:三种改性剂均能与电气石粉表面成功接枝改性,使用KH-570、Si-69和Al-60改性的胶料质量损失率分别为6.50%、11.07%和13.25%。三种改性剂均能使NR/电气石粉的加工安全性能和加工流动性提升,使用KH-570和Al-60还能使胶料的正硫化时间缩短,硫化效率提升。三种改性剂改性后的胶料定伸应力、拉伸强度和撕裂强度均较未改性的明显上升,但断裂伸长率却下降。综合来看,使用Al-60改性电气石粉效果最佳。其中,t10延长了119s,t90缩短了92s,拉伸强度提升了38%,滚动阻力下降了68.97%,动态生热下降了73.33%。
改性剂:硅烷偶联剂γ-缩水甘油醚氧丙基三甲氧基硅烷(KH-560),用量为5%,KH-560预水解pH值为7,KH-560预水解时长1h,反应温度60℃,反应时间1h,搅拌速率1500r/min。
改性方法:配制醇水比为1:8的溶液,加入适量的KH-560(KH-560:醇:水=20:9:72),搅拌均匀,使用40%的乙酸调节pH值,水解一段时间后备用。在磁力搅拌下,将微米Al2O3充分分散于适量乙醇中,混合时间约1h,将一定量(偶联剂用量为硅烷偶联剂占加入氧化铝的重量百分比)预水解后的KH-560缓慢加入到分散均匀后的微米氧化铝中,在不同的条件下混合反应。反应结束后抽滤,用乙醇洗涤三次,在60℃下干燥3h,冷却,密封保存使用。
改性效果:红外光谱(IR)结果表明,KH-560已经成功接枝在氧化铝粉体表面,改性后的氧化铝粉体的棱角圆滑,颗粒无明显团聚现象。改性后氧化铝粉体的吸油值比未表面改性的Al2O3低,下降了43.4%左右。改性后填充环氧树脂,复合材料的黏度降低约16.1%。
改性方法:称取10g氧化铁黄颜料于500mL烧杯中,加入200mL蒸馏水配成浆液,置于60℃恒温水浴锅内,高速搅拌分散30min。取适量钛酸酯偶联剂置于无水乙醇中超声溶解。然后将上述溶液缓慢滴加于氧化铁黄颜料浆液中,在35℃温度下反应0.5h,反应结束后抽滤,并用蒸馏水洗涤数次,80℃烘干得到改性氧化铁黄颜料。
测试与表征:SEM、XRD、FT-IR、分散性、接触角。
改性效果:改性后氧化铁黄颜料结构完整,表面明显具有有机改性基团。在温度为50℃,钛酸酯偶联剂用量为11%,反应2h条件下,改性后氧化铁黄的吸光度值达到0.925,明显高于氧化铁黄颜料的吸光度值(0.471)。分散性实验表明,钛酸酯的改性效果优于铝酸酯改性效果。接触角测试发现,改性后氧化铁黄颜料的接触角都大于90°,且铝酸酯改性后氧化铁黄颜料的疏水性优于钛酸酯的改性。
改性方法:将称量好的200g勃姆石加入高速搅拌器后,向其中加入用异丙醇稀释的钛酸酯偶联剂TC‐114进行表面改性;搅拌10min后,放入40℃烘箱烘0.5h。
测试与表征:制备PP/改性勃姆石复合材料,采用热重分析仪、差示扫描量热仪、极限氧指数测试仪、锥形量热仪等测试复合材料性能。
改性效果:经过偶联剂处理的勃姆石填充PP后所得的复合材料的弯曲强度与纯PP对比的提高了14.4%,冲击强度提升了30.6%,而与未改性勃姆石填充的复合材料比弯曲强度提高了6.9%,冲击强度提升了5.7%,且断裂伸长率相较于未改性的复合材料提升4倍;改性勃姆石填充聚丙烯复合材料的熔体流动速率、热稳定性以及极限氧指数相较于纯PP都有较大程度提升;改性后的勃姆石有增强聚丙烯力学性能性能的效果,并且随着填入量的增加,热稳定性和阻燃性能都随之提高。
改性剂:异丙基三(二辛基焦磷酸酰氧基)钛酸酯偶联剂、硬脂酸、硬脂酸镁、十六烷基三甲基溴化铵及十二烷基硫酸钠等表面活性剂。
改性方法:(1)钛酸酯偶联剂改性,称取5.09未改性云母钛珠光颜料于250mL三口圆底烧瓶中,加入10mL异丙醇,一定温度下搅拌分散15min,再加入溶有一定量钛酸酯偶联剂的10mL异丙醇溶液,继续水浴加热搅拌、回流一段时间。反应结束后趁热抽滤,用异丙醇洗涤,滤饼于80℃下烘干24h,最后过筛得到钛酸酯偶联剂改性的云母钛珠光颜料。(2)表面活性剂改性,称取干燥后的10g云母钛珠光颜料粉末,置于250mL三口圆底烧瓶中,依次加入30mL的无水乙醇和一定量PH=3~4的助剂溶液(如:粘土浆体的水溶液则用冰醋酸或盐酸调节水溶液PH=3~4),超声2-5min分散后,于一定温度下恒温水浴搅拌锅30min后缓慢滴加0.39聚二甲基硅氧烷和一定量表面活性剂的醇溶液(10mL),继续恒温搅拌一定时间后真空抽滤,样品置于烘干箱70℃~80℃恒温干燥24h,最后过筛(150目)可得到表面活性剂改性的云母钛珠光颜料粉末。
测试与表征:沉降曲线、亲油化度值、活化度、吸油量、SEM、XRD、FT-IR等。
改性效果:使用异丙基三(二辛基焦磷酸酰氧基)钛酸酯作为改性剂,通过活化指数和吸油量测试结果表明,规定反应体系溶剂用量为20mL时,改性剂用量为4%,反应温度60℃,反应时间1.5h,对云母钛珠光颜料粉体的表面改性效果较佳;钛酸酯偶联剂以化学键合的方式接枝于云母钛珠光颜料粉体表面;云母钛珠光颜料经钛酸酯偶联剂改性后,其表面接枝了一层有机膜层,由亲水性转为疏水性,具有良好的分散性。用硬脂酸和硬脂酸镁改性云母钛珠光颜料的最佳工艺为反应时间t=2h、反应温度T=70℃和用量2.0%;十二烷基硫酸钠(SDS)改性时,最佳的反应参数为时间t=2.5h、温度T=60℃和用量3.0%;十六烷基三甲基溴化铵改性时,最佳反应参数时间t=2.5h、温度T=70℃和用量2.5%;不同表面活性剂改性云母钛珠光颜料,具有不同程度的疏水亲油能力及分散能力,其中以硬脂酸及硬脂酸镁改性的效果最为理想。改性后的珠光颜料粉体,通过亲油化度、沉降体积和在水/油相中等测试表明其和有机相的相容性明显优于未改性珠光颜料;XRD图表明了经过改性后的云母钛珠光颜料,虽然具有良好的亲油疏水效果,但其晶体结构仍没被破坏,所以仍保留云母钛珠光颜料原有金黄色光泽的物理性质;红外谱图和电镜分析表明,改性后的云母钛珠光颜料表面接上了亲油基的官能团。未改性的云母钛珠光颜料易团聚,经过改性后使其表面吸附有一些粘土浆体中的纳米颗粒,这不仅使得了云母钛珠光颜料具有良好的疏水效果,同时也能改善喷涂时吸附负电荷的能力,增强漆膜的珠光效应。
改性方法:(1)硅烷偶联剂改性,将无水乙醇与去离子水按体积比4:1混合后,加入硅烷偶联剂KH-560搅拌混合制备成改性液。改性液经盐酸或氢氧化钠调节pH值后在40℃下水浴加热静置1h以进行预水解。预水解完成后将改性液与片状锌粉按质量比4:1的比例混合,在一定温度下以400-500r/min的速度搅拌,冷凝回流反应一段时间后,锌粉经抽滤、2次乙醇洗、2次水洗、120℃烘干1.5h、研磨、过100目筛后完成改性锌粉的制备。(2)硝酸铈改性,将无水乙醇与去离子水按体积比4:1混合后,加入硝酸铈制备成硝酸铈改性液,调节pH值为7。将改性液与锌粉按质量比4:1混合后,在25℃下以400-500r/min的速度搅拌改性1h,锌粉经抽滤、2次乙醇洗、2次水洗、120℃烘干1.5h、研磨、过100目筛后完成改性锌粉的制备。(3)复合改性,按KH-560用量12%,pH值为8制备改性液,在改性液预水解完成后加入0.01%质量分数)硝酸铈,60℃下反应1h,锌粉经抽滤、2次乙醇洗、2次水洗、120℃烘干1.5h、研磨、过100目筛后完成改性锌粉的制备。
改性效果:KH-560改性锌片/锌粉的最佳工艺条件为KH-560用量为锌粉用量的12%,反应温度为60℃,pH值为8,反应时间为60min。硝酸肺改性锌片/锌粉在反应温度为25°C、pH值为7、反应时间为60min的工艺条件下的最佳用量为0.010%。KH-560、硝酸铈改性后锌粉在水中的分散性得到显著提高。改性后锌粉制备的涂层表面光滑,未发生明显的锌粉团聚现象。KH-560改性锌粉制备的涂料施工性差,硝酸铈改性锌粉制备的涂料施工性好,且硝酸铈改性锌粉静置2h后仍可完成涂敷;相比于未改性涂层,KH-560改性涂层表干时间和实干时间缩短25%,附着力最好,硝酸铈改性涂层附着力最差。硝酸铈、KH-560改性、硝酸铈+KH-560改性涂层的腐蚀电流密度约降低为未改性涂层腐蚀电流密度的1/16、1/6、1/9。硝酸铈、硝酸铈+KH-560改性涂层相对于未改性、KH-560改性涂层钝化电位区间更大,钝化电流更低,硝酸铈改性涂层具有最低的钝化电流和最小的腐蚀速率。长效保护建议采用硝酸铈改性锌粉。
改性剂:阳离子型聚电解质聚二烯二甲基氯化铵(PDADMAC)、阴离子型聚电解质聚苯乙烯磺酸钠(PSS)、非离子型表面活性剂十八胺聚氧乙烯醚(AC1830)。
改性方法:(1)PDADMAC和PSS改性SiC粉体的过程如下:PDADMAC或PSS和SiC粉体在去离子水中搅拌6h,然后在3500rpm下离心10min。离心后的粉体在90℃下干燥12h,以获得聚电解质改性的SiC粉体。(2)十八胺聚氧乙烯醚与聚苯乙烯磺酸钠联合改性碳化硅,使用磁力搅拌器将50g原始碳化硅粉末和50ml去离子水混合;将混合物搅拌0-6小时;添加0.1-1.5wt%的AC1830(基于SiC粉体的质量),并将浆料搅拌0-6小时;为了尽可能减少改性剂过多造成的负面影响,以3500rpm的速度离心浆料5min,去除上清液,将沉淀物重新分散在50毫升去离子水中,然后再次离心;将沉淀物在90℃的烘箱中干燥12h,研磨后获得经AC1830改性的SiC粉末;使用PSS重复上述操作;将改性后的碳化硅粉末均匀地分散在去离子水中,得到改性碳化硅浆料。
测试与表征:SEM、XRD、粒度分布、浆料粘度、固相含量、Zeta电位、浆料沉降稳定性、表面吸附量。
改性效果:(1)聚二烯二甲基氯化铵(PDADMAC)通过静电引力相互作用吸附到SiC颗粒的表面。由于二者间的高亲和力吸附作用,PDADMAC在SiC表面的吸附构型为平坦的构型,且吸附量、吸附构型及改性效果不随分子量的变化而变化。改性pH值为11,添加量为0.24wt%,温度为90℃,改性时间为6h。由于PDADMAC的吸附使得SiC表面的电荷反转,将改性SiC粉体溶于水介质中调节pH值至3,改性SiC粉体通过静电-空间位阻稳定机制均匀分散在水介质中,制备了50vol.%固相含量下粘度为0.138Pa.s的SiC浆料。
(2)聚苯乙烯磺酸钠(PSS)通过氢键和范德华力相互作用吸附到SiC颗粒的表面。由于二者间存在静电排斥相互作用,PSS在SiC表面的吸附构型为环状和尾状的构型,且随着PSS分子量的增大其在SiC颗粒表面的环状构型扩大、吸附量增大、改性效果变好。采用分子量为Mw=1000000的PSS,改性过程中不调节pH值,添加量为0.3wt%,温度为90℃,改性时间为6h。将改性SiC粉体溶于水介质中,调节pH值至11,改性SiC粉体通过静电-空间位阻稳定机制均匀分散在水介质中。得到了较高固相含量(45vol.%)的SiC浆料,对应的浆料粘度为0.098Pa.s。
(3)采用非离子型表面活性剂十八胺聚氧乙烯醚(AC1830)和阴离子型聚电解质聚苯乙烯磺酸钠(PSS)作为改性剂对碳化硅粉体进行改性。AC1830的吸附不受表面电荷的影响,能屏蔽部分电荷,且可作为PSS的吸附位点,促进PSS在SiC表面的吸附。制备了粘度为0.039Pa.s、固相含量为50vol.%的适合于注浆成型的SiC浆料。Zeta电位法表明,用该方法改性的SiC粉末的等电点(IEP)明显向左偏移。沉降实验表明,分散稳定性显著提高。接触角测量表明,改性剂成功地吸附在粉末表面,并提供亲水基团,从而改善了粉末的润湿性。吸附测试结果表明,PSS对SiC粉体和AC1830改性SiC粉体的等温吸附模型和动力学吸附模型符合Langmuir模型和伪二级(PSO)模型。AC1830在SiC表面的吸附提高了PSS的吸附能力。
改性方法:将三聚磷酸铝、ZnO和去离子水混合,在高速分散机下常温搅拌30min(1000r/min),通过ZnO改善三聚磷酸铝表面高酸值特性,之后将上述悬浮液转移至恒温水浴锅,加入单宁酸,KH-550,恒温60℃搅拌12h,反应完成后,使用去离子水与酒精溶液反复清洗3次去除残余的改性物质后,烘干(105℃)、粉碎得到改性三聚磷酸铝防锈颜料。
改性效果:ZnO有效地缓解了三聚磷酸铝的高酸值特性,改性三聚磷酸铝的pH提升,H+被抑制释放导致三聚磷酸铝的电导率略微下降,同时ZnO与单宁酸改性,造成了三聚磷酸铝的吸油值下降。盐雾试验证明1%单宁酸改性的三聚磷酸铝(单宁酸@三聚磷酸铝-1)在水性丙烯酸中的防锈性能最佳,过量的单宁酸改性造成防锈颜料的防锈性能下降,单宁酸/硅烷偶联剂有效地改善了三聚磷酸铝与丙烯酸树脂之间的相容性。激光粒度仪表明改性后三聚磷酸铝有少量颗粒聚集,但不影响在涂料中的使用;SEM表征说明三聚磷酸铝表面并非连续聚集状态,三聚磷酸铝表面有一层不规则包覆层,这是ZnO/单宁酸/偶联剂改性三聚磷酸铝在其表面反应形成的。FT-IR分析表明单宁酸负载在三聚磷酸铝表面,XRD分析结果说明ZnO的添加与主物质三聚磷酸铝反应,形成更多非主物质三聚磷酸铝可溶性物质。
改性剂:十六烷基三甲氧基硅烷,十二烷基三甲氧基硅烷,癸基三甲氧基硅烷与辛基三甲氧基硅烷。
改性方法:将平均尺寸为约1-2μm的铝填料180g添加至300ml的无水乙醇中,并将混合物在室温下搅拌2小时;随后添加不同的硅烷偶联剂(铝填料的重量为5%)和15ml去离子水添;将样品在75℃下冷凝并回流,并搅拌5小时;将样品以8000RPM离心10分钟,然后用无水乙醇重复离心洗涤多次,以确保完全除去未反应的硅烷偶联剂。然后将样品放入真空烘箱中,并在120°C下真空干燥5小时备用。
测试与表征:SEM、XRD、FT-IR、TGA、接触角等
改性效果:表面化学性质处理的铝填料显著提高了热界面材料的性能,其中粘度可降低77%,断裂伸长率可达154.71%,导热系数也有所提高,热均匀性显著提高,在极端冷热循环条件下,热稳定性提高了近20%。同时,降低铝填料的表面能有利于提高铝填料在有机硅基体中的分散性。不同硅烷偶联剂改性的导热填料对填料的分散以及导热复合材料的性能有较大的影响。使用十二烷基三甲氧基硅烷偶联剂的改性的铝填料及其制备成的热界面材料的综合性能最为优异。
由【粉体技术网】编辑整理,转载请注明出处。
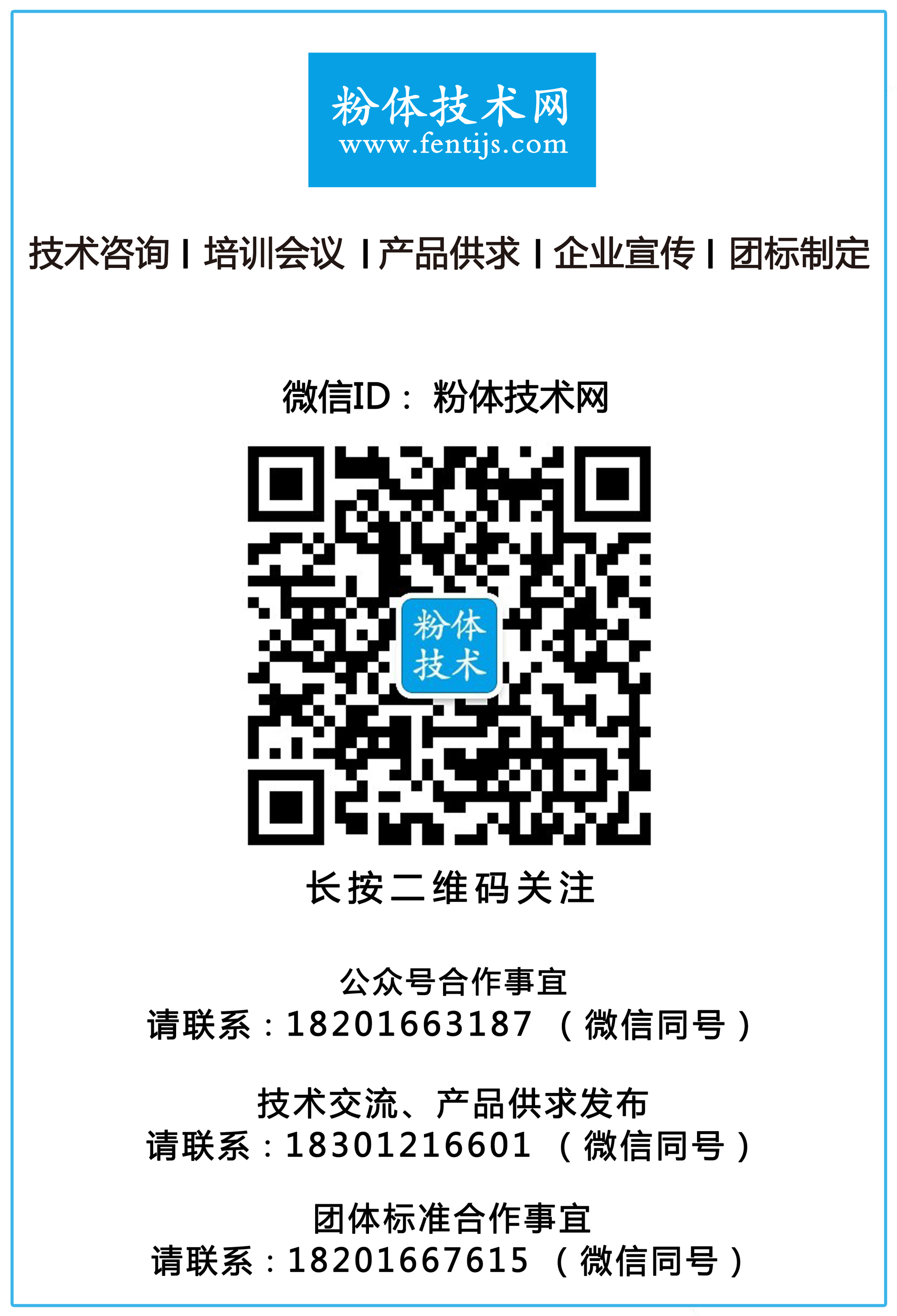
|
|
|
|
|
|
|
|
|
|
|
|