目前,重质碳酸钙加工企业多采用立式磨、球磨机和雷蒙磨等装备,雷蒙磨适宜400目以下粉体的加工,球磨机较适宜800~1250目超细粉体的生产,而立式磨适宜1250目以下非金属矿粉体的规模化加工。
立式磨规模化和节能效应显著,在很大程度上实现产品的精细化生产的同时,具有操作简单、维护方便、工艺布置简单、占地面积小、土建投资低、噪音小、环保性好等优势,已成为当下重质碳酸钙等非金属矿粉体加工技术研究的新进展之一。
下面,就结合重质碳酸钙HRM高细立式磨粉磨工艺,探讨重质碳酸钙立式磨粉磨工艺及影响因素,以期供生产、工程技术人员借鉴参考之用。
1、重质碳酸钙立式磨生产工艺
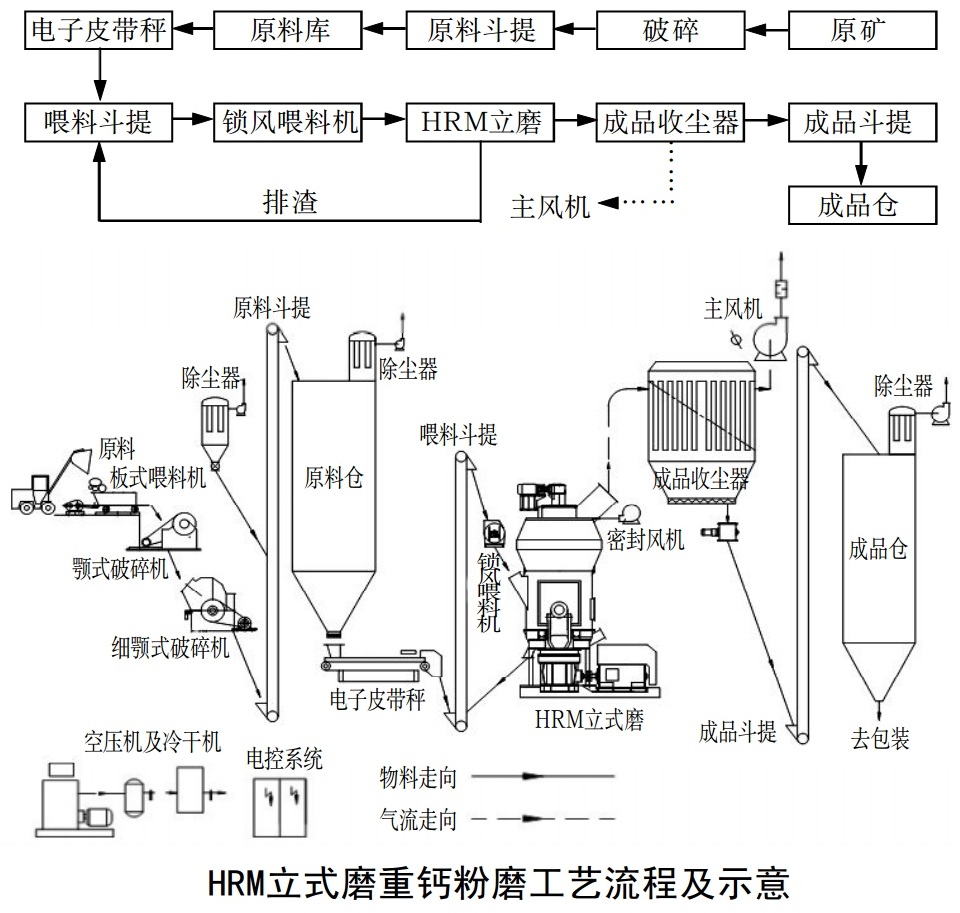
工艺说明:
原矿由铲车喂入振动板式喂料机,经破碎机破碎后由提升机提升送入原料储库待用。
来自原料储库的物料,由变频控制的电子皮带秤定量经喂料提升机和锁风喂料机送入旋转的立式磨磨盘中心,在离心力作用下,物料向磨盘边缘移动,进入粉磨辊道。
磨辊在液压装置和传动臂的作用下,向辊道内物料施加压力,物料受到破碎、剪切、挤压和粉磨作用。
同时,风从磨盘边缘的风环处高速均匀向上喷出,外溢物料被高速气流吹起,大颗粒落入磨盘,细颗粒经选粉机进行分级;
合格细粉随同气流出磨,由高效脉冲袋式收尘器收集为成品,经成品提升机(或气力输送)送入成品仓,用包装机(小袋/吨袋)进行包装入库;
不合格的粗粉在选粉机叶片作用下重新落至磨盘,与新喂入的物料一起重新粉磨。
磨机回料经喂料提升机再次喂入立式磨粉磨,如此循环,完成粉磨、分级作业全过程。
2、影响立式磨操作与运行的因素
(1)入磨物料硬度
方解石硬度一般在2.8~3.0之间,因原矿中夹杂物的种类、含量不同而有所区别。通常而言,物料硬度高,易磨性差,磨耗高,因此物料硬度直接关系到产品产量和磨机耐磨件的使用寿命。
(2)入磨物料粒度
物料的粒度可根据成品细度来进行合理控制,原则上是“多破少磨”。
立式磨对于原料的粒度有一定的范围要求,粒度过大或过小都会破坏磨盘上料层的级配平衡,不利于磨机的正常运行:
若进料粒度过大,使得一次研磨效率降低,增加物料的循环次数,无形中增加磨机的粉磨功耗,同时,因缺少细颗粒物料的缓冲,导致磨机振动加大。操作中遇到此问题宜进行适当的减料,稳住磨机压差和料层。
若进料粒度过小,其粉状料必然增多,由于细颗粒附着力差,加上内部气流作用,料床流态化趋势明显,使立式磨不能有效地啮入大量的颗粒群,造成料层不稳,导致磨机振动。
在非金属矿粉体行业,产品细度一般相对要高(常用的重质碳酸钙粉d97=325~1250目,即10~45μm,97%通过)。对于入料粒度的控制建议宜小一些(<30mm),这样更有利于发挥立式磨的超细研磨特性,做到产能最大化。基于调试经验,入磨物料的最大粒度不宜超过磨辊直径的3%,可适当再控制小些。
(3)入磨物料含水量。
入磨物料含水量的控制对立式磨的稳定运行至关重要。通常,重质碳酸钙微粉生产线未设计热风系统(原料含水量一般<3%),热能主要由磨机内的物料碾磨、摩擦及空气流通产生。磨机在碾磨过程中,料床上有大量没有被气流及时带走的成品和不合格细粉,若原料含水量过大,新入磨物料会粘结料床上的细粉,造成磨盘上形成料饼,在持续喂料的情况下,会造成磨盘料层不断增厚,致使磨辊无法对物料有效碾压和粉磨,磨机由于负荷过大产生振动或振停。
(4)入磨物料易磨性
入磨物料的易磨性直接关系磨机产量、电耗和辊套衬板的使用寿命。方解石原料邦德功指数通常在9~11kW·h/t,数值越小,物料越易粉磨。
与此同时,立式磨的喂料要求稳定、连续,调节时力求渐增或渐减。若喂料量出现大的波动将会打破磨内物料的动态平衡,引起料层波动,使磨盘物料研磨不均匀受力,易导致磨机振动。
立式磨研磨重质碳酸钙粉时的料层厚度一般在30~40mm为宜,不宜过厚,否则达不到超细研磨效果。通常,料层厚度为磨辊直径的2%±20mm(水泥生料行业的经验规律),对于非金属矿行业可以控制小一些。
(5)磨机压差
磨机压差是反映磨机内部物料循环负载情况的重要参数之一,正常工况下磨内压差应是稳定的,即在一个范围内处于趋稳变动状态,这标志着进入立式磨的原料量和出磨成品量达到了一个动态平衡,一旦这个平衡破环,磨内循环负荷发生变化,压差就会突增或突减,若得不到及时有效控制,将影响磨机的稳定运行。
影响磨机压差的因素很多,如物料易磨性、喂料量、系统风量、研磨压力、选粉机转速等。凡是影响磨机平稳运行的因素,几乎都可以在压差上反应出来。
压差增高表明入磨原料量大于出磨成品量,磨内循环负荷增加,此时喂料提升机电流变大,排渣量增大,此时从磨机限位装置可以判断料层在不断增厚。为保证产品细度合格,一般不对分离器转速做调整(或者在不影响细度情况下可适当降低转速)。通常做法是做减料、短暂性断料处理,待磨机压差恢复平稳,再稳定增加喂料至合理值;或者在磨机主电机负载允许范围内不做减、断料处理,适当提高辊压,增加粉磨能力,避免磨机出现“饱磨”情形,因负载过大产生振动。
压差减小表明入磨原料量小于出磨成品量,磨内循环负荷降低,此时喂料提升机电流减小,排渣量减少,此时从磨机限位装置可以判断出料床在逐渐减薄。此时可以采取加料、减压或者降低风量等措施,避免磨机出现“空磨”情形,因料层太薄而产生振动。
根据调试经验来看,在同等工况下,产品细度越细,则磨机压差也越高,反之为低。实践中立式磨的诸多运行参数是相互关联的,操作时应注重参数之间的动态协调。
(6)系统通风量
HRM立式磨在负压下操作,其物料输送、烘干、分级均需大量的风,合适的磨内通风量是磨机稳定运行的必要条件。磨机运行时的通风量则直接影响产品的产量及细度:
通风量大,磨内风速增加,烘干及输送物料的能力增强,磨机内、外循环量减少,料床上粗颗粒增多,料层较薄,磨机产量提高;
若风量过大则可能导致产品细度不合格(跑粗)或产品细粉含量降低(循环次数少,粉磨时间短),品质下降,磨机也会因料层过薄而产生震动;
通风量小,磨内风速降低,烘干及带料能力减弱,磨机内、外循环量增大,料层较厚,磨机粉磨功耗增大,产品细度较细,但磨机产量降低,同时磨机也会因料层过厚负载太大而可能引起振动或振停。
立式磨系统通风量主要通过风机风门的开度(或风机电机变频调速)来调节,立式磨本体、收尘器和通风管道的漏风对磨内通风影响很大,常常是造成产量下降和运行不稳的因素。
根据现场调试经验,生产d97=400目以下重质碳酸钙微粉时,立式磨排渣一般为少量颗粒及粉料,此时只要保证喂料、风量的合理、平稳渐增,立式磨运行较稳定;生产d97=600目以上微粉时,物料需要在立式磨内进行循环多次的研磨和分级,因此立式磨排渣口会产生较多细粉,宜控制好合理的喂料量和风量,在排渣量较稳定时可适当微增风量,提升带料能力,待排渣量减少时可微增喂料量,以保证磨机运行在内外循环的动态平衡下。
(7)磨辊的工作压力
磨辊的工作压力需根据喂料量、料层厚度、产品细度等因素进行合理给定,压力过小达不到有效粉磨,出粉率低,产量低;压力过大则可能导致料层不稳,可能对减速机造成不必要的损害。
根据项目调试经验,立式磨生产d97=600目重质碳酸钙微粉,磨辊最佳工作压力在13~14MPa为宜。
(8)分级机的转速
HRM高细立式磨顶部自带动—静态高效分级机,可以灵活地调节产品细度及颗粒级配分布,
调整范围大,适应性好。
分级机的技术参数主要包括:转子直径、转子高度、转子叶片角度、转子叶片数量、导风叶片(静叶片)角度及转子转速。转子直径和高度依据磨机型号不同而专门设计(合适的径高比)。通常,导风叶片角度根据工况定期在停磨时调整,转子叶片角度及数量在设备选型时决定(根据产品特性、细度要求定),生产环节调节转子转速即可。成品细度主要取决于转子转速和系统通风量大小。在系统通风量一定的情况下,转子转速高,出磨物料细度高;反之,生产粗粉时,需降低转子速度。
在生产调试期间,针对不同系列的产品摸索出选粉机转速经验值后,后期生产在经验值上做适当微调即可,立式磨的操作便捷和生产灵活性显而易见。在实际生产中,由于选粉机顶部的间隙易造成产品细度跑粗问题,针对此情况,HRM高细立式磨在选粉机的顶部密封上采用独有的气体密封方式,能够有效地阻止粗颗粒通过。
(9)挡料环高度。
挡料环的高度直接影响磨内料层的稳定及粉磨效率。挡料环的高度过高,不利于磨床上的物料外溢,导致料床增厚,一部分合格的成品在料床上也不能被气流及时带走,造成过粉磨;挡料环的高度过低,则粉料外溢速度加快,造成料床过薄,导致磨辊不能加压或造成磨机振动。
根据调试经验,HRM高细磨在生产d97=600目重质碳酸钙粉时,为保证研磨的有效性,入磨物料需要在磨床上有一定的停留时间,挡料圈的高度一般设置在30~50mm为宜。
(10)风环间隙(面积)。
在实际生产中,常发现磨机回料量比较大,但是立式磨运行还算稳定,此时可以适当缩小风环间隙(在挡料环或上风环外缘补焊圆钢)面积,提高风环处风速,增加带料能力,减少排渣量,起到一定的提产稳产作用。
(11)磨辊与磨盘的磨损。
根据项目情况来看,当磨机运行很长时间(重质碳酸钙行业一般3~5年)后,磨机产能会有一定程度的下降,主要原因是由于磨辊和磨盘磨损造成的,导致辊盘研磨区域的研磨结构、研磨压力都发生了变化。
辊盘磨损问题对于细度要求高的成品来说,产能骤降更加容易体现。此时,宜对辊套进行调面处理,重新堆焊(堆焊辊套适用)或者更换新的辊套和磨盘衬板(产能降低10%以上就应该考虑以上措施)。
总之,立式磨用于非金属矿粉体行业,展现了其规模生产和精细加工的双重特性,逐渐顺应了非金属矿粉体领域未来的发展趋势,其优良的性能带动了粉体加工装备的技术升级,利于提升非金属矿粉体的经济附加值水平。
来源:崔啸宇,李晓光,郭凌坤,等.重质碳酸钙立式磨粉磨工艺及操作浅析[J].中国非金属矿工业导刊,2014(1):37-40.
更多精彩!欢迎扫描下方二维码关注中国粉体技术网官方微信(粉体技术网)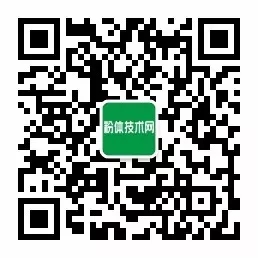
|