(中国粉体技术网/班建伟)随着国家对环境保护要求的日益严格,现有和新建燃煤含硫量大于 1% 的电厂必须建设脱硫设施。电厂脱硫工艺主要以石灰石/ 石灰—石膏湿法工艺为主,约占总容量的 86%。湿式制粉设备为湿式球磨机,干式制粉设备为立式辊磨机 (简称立磨)。
立磨为料床粉磨,与球磨机相比具有入磨粒度大、粉磨效率高、单位电耗低及节能环保等优点,比球磨机节能 40%~50%。另外,立磨系统为负压操作,工作环境清洁,没有湿式球磨机废水、废渣的环境污染,符合国家节能减排、安全生产的要求,目前立磨在脱硫制粉工艺中逐渐呈现出主导设备的趋势。
原有集中加载方式的立磨存在规格大、产能低、选粉效率低及工作不平稳等问题,已经难以适应脱硫制粉大型化的要求。针对上述问题,北方重工集团成功开发出新型结构的脱硫立磨,并已经得到生产应用,设备运转良好。
1 单辊加载立磨的技术特点
脱硫石灰石粉成品细度要求 45 μm (325 目) 筛余10%,远高于水泥生料成品细度要求 (180 μm (80 目)筛余 14%)。物料成品细度越高,需要的碾磨压力越大;产量越高,要求的选粉能力越强;物料含水量低,磨机进出口压差需要保持平衡,入出磨温度需要控制,这都给单辊加载立磨提出了更高的技术和工艺要求。
1.1 单辊加载
改变传统集中加载模式,采取单辊高压楔形加载系统 (见图 1),将粉磨压强提高了 1 倍 (见表 1),克服了集中加载加载力不均、振动大和碾磨比压小的缺点。采用强力增压粉磨机构,优化设计合理的磨辊和磨盘瓦的曲率;磨辊磨盘之间设计有楔形间隙,形成增压区和高压粉磨区。在增压区内迅速压实松散物料,并完成初碎和粉磨,在高压粉磨区内完成物料终粉磨,解决了高压粉磨存在压力释放的难题,提高了碾磨效率。
1.2 选粉效率
采用新型高效动静态选粉机,使选粉效率达到90% 以上。运用惯性选粉、重力选粉和离心选粉原理,设计最优的分离通道,并采用先进的反向叶片密封技术,在低转速下即可达到理想的分离效果。这不仅提高选粉效率,并且能够有效减小磨机的通风阻力,降低系统风机电耗,而且采用变频调速可使得细度调节范围变宽,适应生产实际工况,从而降低磨机内的循环负荷。
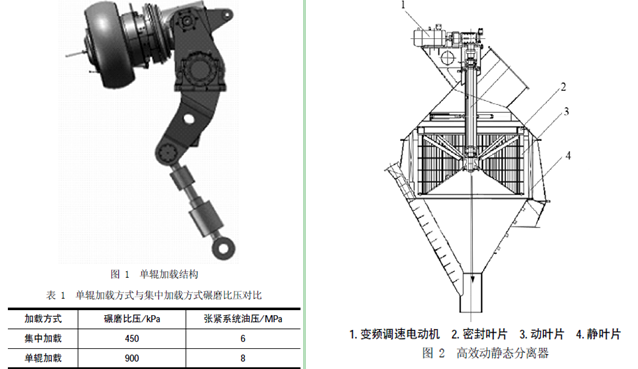
1.3 稳定料层技术
石灰石物料含水量低,粉磨时磨辊和磨盘间的料层不易稳定,直接导致磨机运转时振动过大。采用稳定料层综合技术,设计可调高度式挡料环,以控制物料在磨盘上停留的时间;使用可调式喷口环以调整风速,达到合适的喷口环风速;控制选粉机回粉量以减少料床上的细粉;配备喷水装置,必要时进行磨内喷水;采用具有减振功能的磨辊限位装置,避免磨辊和磨盘由于料层不稳定而导致的直接接触。在多种手段综合作用下,单辊脱硫立磨的运行非常平稳。
1.4 立磨调试
在设计过程中,通过工艺平衡计算和对立磨进行工艺试验等手段,初步确定了最佳脱硫立磨工艺参数,特别是风量、局部风速、压力与磨机产量、成品细度以及分离器转速等的匹配关系。在立磨调试时发现,如果磨机内粉磨过的物料不能及时排出,致使磨机内部物料过多,磨机负荷增大,料层不稳定,会导致立磨振动过大。单辊加载的磨机在调试时,几乎不必考虑加载力的稳定情况,仅通过调整风料配比就可在很短的时间内使立磨正常运转。
粉磨系统中与立磨相关的其他设备对磨机工作影响较大的是收尘器。立磨运转时,如果袋式收尘器压差过大,将导致细粉不能排出,磨机内过饱和,最后振动停机。在条件具备的前提下,单辊加载的立磨调试时间仅为 5~7 d。
单辊加载立磨与相近规格集中加载立磨相比,磨机的产量得到了大幅度的提高。表 2 表明单辊加载立磨完全实现了小规格、大产量的突破。
2 应用成果
某公司于 2009 年购买了 2 台 MLT2650 型脱硫立磨,于 2010 年投产,设备运行稳定,达产达标。在该设备成功应用后,北方重工集团有限公司又成功开发出 MLT3250 型脱硫立磨,单机产能达到 100 t/ h,用于山东魏桥铝业公司脱硫岛项目。
3 结语
石灰石粉—石膏法是当前我国主流脱硫工艺,大型脱硫立磨可以取代传统球磨和小型立磨作为该工艺的主机设备。若我国脱硫设施全部采用该种设备,每年可制备石灰石粉 3 250 万 t,减排 SO2 2500 多万 t,相比球磨系统节电 2 亿 kW·h,并打破传统的制粉模式,可在矿山就地建设大型干式脱硫制粉厂,供应周边多个电厂,相比每个电厂都建小型脱硫制粉系统,规模效益十分明显。因此脱硫立磨的研究制造,对于我国加强环境保护,减少污染具有相当大的意义。
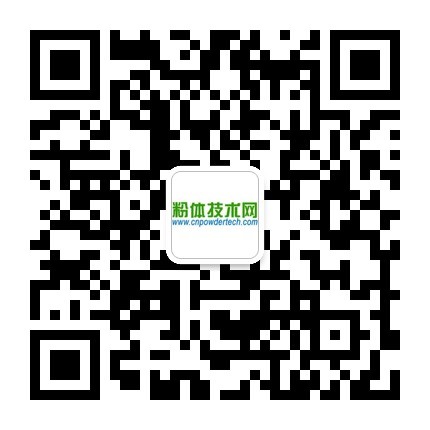
|