1 引言
碳酸钙是应用很普遍的工业添加剂,目前国内产能满足市场需求但还有一定的空白,一些产品尤其高品质的碳酸钙需要从日本或台湾等国家地区进口。随着国内对矿产资源利用的进一步发展,优质的石灰矿不断被发现和利用,碳酸钙产业的新建厂需求和产品品质提升改造蓬勃发展。选择合适的工艺技术是碳酸钙生产企业适应市场优胜劣汰的关键,本文将以年产5万吨的碳酸钙生产工艺进行剖析,以期对碳酸钙企业生产技术的提升有一定的启发和帮助。
年产5万吨的碳酸钙生产工艺分为石灰煅烧工序、消化工序、窑气净化工序、碳化工序、脱水工序、干燥包装工序等工艺流程图如图1所示。
2 石灰煅烧工序
煅烧工序对于碳酸钙的生产非常关键,所产的石灰和窑气都是后续工序的原料,本工艺要求石灰具有中等活性,窑气浓度稳定。所以碳酸钙生产应优先选用优质石灰矿,经过900~1100℃高温煅烧得到的中等活性的生石灰,这样才能保证消化的灰浆细腻、活性好。石灰石的质量对工艺的影响很大,其中的杂质SiO 2 、AL2O3 、Fe2O3等不仅会影响化灰速度、脱水速度,降低生产效率,还会影响产品的纯度、白度等指标。
注:1#线生产纳米碳酸钙;2#线生产活性碳酸钙;3#线生产轻质碳酸钙。
图1 碳酸钙生产工艺流程简图
煅烧设备选用机械化立窑,该窑从计量配料、上料布料、出灰全部实现自动化,系统采用PLC控制,可以对投料量、出灰量、煤石配比、各段煅烧温度、给风量进行监控和记录,控制CaO的烧成率及活性,二氧化碳气体浓度可达30~35%以上。自动化程度高,节省人工且CaO品质好、产量高。
3 消化工序
快速消化有利于形成更加细腻的Ca(OH)2浆料,消化用水的温度对消化速度的影响很大,1250℃煅烧石灰,若用水温度为20℃消化,其消化时间为65分钟,当水温为40℃时消化时间为11分钟,而水温在80℃则只需3分钟。本工艺采用50~70℃的热水化灰,热水用回收窑气的热量产生,既节能又满足工艺需求。
除渣精制后的熟浆进行一定时间的陈化是非常必要的,在消化过程中有一些CaO的小颗粒被Ca(OH)2包覆,在碳化过程中常常不能及时释放出来参与反应,导致产品出现“返碱”现象,影响产品质量。目前国内碳酸钙行业采用的生浆陈化方式一般为静态陈化,陈化池容积小、个数多。此种工艺不仅陈化效果差,还易造成产品质量不稳定。
动态陈化,即采用大型陈化池,利用搅拌机的高剪切力使精浆更加细腻,采用污水泵使精浆强制循环。该工艺减少了精浆的热损失,较高的陈化温度还可以缩短陈化时间,进而减小陈化池的容积,节省空间。重要的是可以有效地防止Ca(OH)2包裹CaO,使得进碳化塔的精浆浓度保持稳定,Ca(OH)2粒度分布窄。一般的熟浆经过15小时以上的动态陈化达到较好的陈化效果。
化灰设备采用回转化灰机,该设备机械化程度高,劳动强度小,连续性强,电耗低。陈化浆池每套采用三座带搅拌的大型浆池,并且用泵强制循环可保证熟浆中Ca(OH)2颗粒在3μm以下。
4 窑气洗涤工序
窑气的净化对碳酸钙生产工艺好处很多,一是减少其中携带的杂质对产品白度的影响,提高产品质量,二是消除杂质、二氧化硫等对管道、设备的腐蚀,降低装置的故障率。因此窑气的净化不仅要除尘还要进行脱硫处理。
传统的窑气洗涤设备运行不平稳,塔板经常因窑气携带的杂质沉积而堵塞,维修费用高。从降低费用和运行平稳的角度出发,除尘装置向“大型化”的方向发展。若采用大型的除尘脱硫装置,一座或多座窑采用一套净化系统即可:即脱硫塔与洗涤塔串联,再加上除雾、除水装置。新型的脱硫塔和洗涤塔采用天津创举公司研制的MP塔盘,这种类型的塔盘传质效率高,处理能力大,压力降小,塔板上无活动部件,结构简单、可靠,不会因磨损、震动等原因造成传质单元脱落,基本上无维修工作量,且操作弹性较大,可在设计能力的60-130%范围内正常开车。河北乾昊集团采用该类型的塔板进行改造后产品的白度从92%提高到94%。
洗涤、脱硫塔采用1波美度的石灰水作为工作液,吸收pH到7以下后用一台过滤面积为50m2压滤机进行压滤,将滤饼经过干燥破碎后用作建筑材料,可作为商品灰粉销售。不仅实现了环保,还提高资源的利用率。
5 碳化工序
碳化反应是整个碳酸钙生产工艺的核心步骤,从产能和产品品质上来讲,碳化反应的速度越快越好。众多的研究表明,碳化反应的快慢取决于CO2的溶解速度。增大气液接触面积和降低温度都可以增大CO2的溶解速度,从而可以提高反应速度缩短碳化时间。一般生产普通轻钙通过在碳化塔中加入搅拌装置来增大气液接触面积就可以达到缩短碳化时间的效果;生产纳米碳酸钙还需要冷冻机降低熟浆温度,碳化过程中还需将反应过程中的放出的热量移走。
通过调整碳化参数和加入晶型控制剂可以生产不同晶型的碳酸钙产品,所生产晶型电镜照片如图2所示。对于镁含量较高的石灰矿,在碳化时增加碳化时间可以降低碳酸钙产品中的镁含量,脱水后的滤液在经过热解可以将滤液中的镁制成碳酸镁作为副产品销售,滤液镁含量下降后可以再去进行化灰,达到水“零排放”的标准。如果产品白度较差则需要进行增白,碳化完毕后利用碳化的余温,在增白槽中加入络合增白剂,进行增白,增白槽设置蒸汽加热装置,如果碳化余温不够,可以进行二次加热。
图2 不同晶型的碳酸钙产品电镜照片
碳化塔中的搅拌采用三层涡轮叶片式的搅拌,如图3所示,通过高速的剪切力有效降低了碳化过程的碳酸钙对Ca(OH)2的包覆,碳化塔的持气量比未加搅拌的碳化塔提高了约3/4,因此窑气中CO2的利用率大大提高,碳化时间缩短,辅以特殊的气体分布器效果更好,碳化塔尾气中CO2的含量由普通碳化塔的8-10%下降到6%以下。综合考虑增加的搅拌电机消耗的电量和缩短碳化时间减少罗茨风机的电量,碳化用电量比普通的碳化塔是降低的。搅拌电机可以加装变频器,调节碳化不同阶段的搅拌速度,可以进一步节约电量的消耗。

图3涡轮搅拌和碳化塔示意图
6 脱水工序
脱水效果好可以有效降低干燥环节的热负荷,减少干燥时间。通常的脱水装置是上悬式离心机,虽然设备投资少,但需要操作工人数多,工人劳动强度大,生产环境恶劣;由于离心机存在漏料的现象,滤液中碳酸钙晶种含量高,滤液回用后使得产品沉降体积小,粒度分布宽,吸油值高;由于洗涤效果差而使得产品镁含量高。
轻钙生产采用全自动卧式刮刀离心机采用PLC和变频器控制进行控制,可按生产需求设定控制加料、脱水、洗涤等工况的转动速度和时间,以物料限位装置和进料自动阀门连锁保护料层厚度,保证不发生“跑料”现象,洗涤完毕后采用液压驱动的刮刀自动卸料。脱水效果良好,滤饼含水率可达到15~20%。很大程度上减少人员的使用和劳动强度,大大提高了劳动效率。
微细、超细碳酸钙选用带洗涤功能的板框压滤机,虽然一次性设备投资大,但操作费用低,工人劳动强度大大降低,生产环境好,脱水效果好。压滤机的洗涤功能不仅可以解决滤饼洗涤降低镁含量的问题,更重要的是其滤液中的碳酸钙晶种含量低,便于调整产品的沉降体积,生产微细、超细碳酸钙产品。
7 干燥包装工序
普通轻质碳酸钙的干燥与筛分设备这几年变化比较大,从最初的热风滚筒干燥机、三层筛粉机的方式已经发展到了目前的带式穿流干燥机、风选机、自动包装机,取得了较好的效果,无论从烟煤的消耗上还是从人工成本上都有了较大的降低。
带式穿流干燥机采用列管间接式燃煤热风炉为干燥热源,保证干燥空气的恒温、恒压、无尘等条件,待干燥物料均匀的分布到不锈钢网带上,热空气自底部进入,经过与物料的多次接触后带走物料当中的水分。网带的移动速度和干燥时间可根据物料的水分和进风的温度自由调节,干燥后的产品连续送出。全系统采用负压操作,减少粉尘对环境的影响。这种干燥方式生产能力大、热效率高、弹性大、自控程度高,是目前能耗低效果好的干燥方式之一。
解聚使用的是气流涡旋粉碎机或者旋风磨等。从能耗及产品质量双重考虑,某些产品直接从二级干燥后不用粉碎就可以使用。高端产品可以加气流粉碎机或者旋风磨等,这样二次干燥、二次解聚,产品团聚体粒径小。在包装方面,为了环境清洁,还是使用自动计量包装机进行分装作业。
随着我国对环保安全的重视,新的法律法规的实施,“三废”的治理成本逐渐升高,碳酸钙企业将面临一场改革,只有采用先进的生产工艺,提高产品的附加值,降低生产成本,提高产品质量,节能环保才能在激烈的竞争中站稳脚跟。该工艺是作者几年工业实践的总结,成熟的工业生产装置在河北井陉已经过多年的运转,事实证明效果良好。
本文作者:何豫基,胡琳娜,盛晨军 (河北工业大学化工学院,天津一化化工有限公司)
►欢迎进入【粉体论坛】
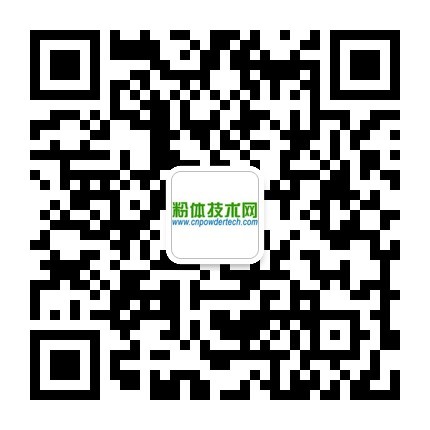
|