(中国粉体技术网/班建伟)石墨按结晶程度分为晶质(鳞片状) 石墨矿石和隐晶质( 土状) 石墨矿石,晶质石墨矿石中石墨晶体直径大于1 μm,呈鳞片状,矿石品位较低,固定碳含量一般不超过10%,局部特别富集地段石墨矿则可达20% 或更多,但可选性好,选矿产品品位能达到90%甚至95% 以上;隐晶质石墨矿石中石墨晶体直径小于1μm,呈微晶的集合体矿石品位高(50%~80%),但可选性差,一般开采后直接出售,因此其工业应用没有鳞片状石墨广泛,市场售价也较低。
石墨自大规模开发利用以来,有关鳞片状石墨开发研究己经很成熟,而隐晶石墨浮选技术在我国尚处于不成熟阶段,有关研究较少,如何开发新工艺使隐晶质石墨的品位得到提高,是值得关注和研究的课题。
1 原矿性质
1.1 矿石化学成分分析
隐晶质石墨来自湖南鲁塘地区,化学成分(w/%)为:C,71.57;TFe,1.3;Fe2+,0.93;Fe2O3,0.52;Cu,0.013;Pb,0.048;Zn,0.056;TiO2,0.38;SiO2,12.99;Al2O3,6.02;CaO,1.31;MgO,0.35;MnO,0.03;Na2O,0.24;K2O,1.15;P,0.085;S,0.28;灰分,25.28;挥发分,3.15。矿石中主要元素碳含量为71.57%,灰分含量为25.28%,主要脉石组分是SiO2 和Al2O3,其次为CaO 和K2O,四者总计21.67%,占灰分量85.72%。有害元素磷、硫存在,含量不高,还有少量铜铅锌等有价金属元素,综合回收价值不大。
1.2 主要矿物含量及嵌布特性
矿石中主要矿物含量(w/%)为:石墨,71.2;石英,8.8;云母,10.2;绿泥石、蒙脱石,6.6;方解石,1.6;黄铁矿、雌黄铁矿,0.4;闪锌矿,0.1;方铅矿,<0.1;黄铜矿,微量;其他,1.0。矿石中主要有用矿物为石墨,且含量最大,矿物晶粒细小,多以集合体形式出现。脉石矿物主要为云母、石英和绿泥石,石英呈细小粒状,粒度一般在0.02~0.1 mm,多与绢云母混杂出现,绢云母多小于0.02 mm,呈微细鳞片状,另有少量蒙脱石、方解石,少量金属硫化物分别是黄铁矿、磁黄铁矿。细小的脉石分布在石墨集合体中或与石墨相间紧密镶嵌,是隐晶质石墨选矿产品品位难以提高的原因之一。
1.3 试验方法
石墨浮选矿浆质量分数在7%~15%比较合适,隐晶质石墨浮选需细磨,矿浆黏度较大,充气条件较差和浮选速度降低,低矿浆质量分数可以改善上述不良影响,本实验矿浆质量分数定为10%。磨矿设备采用ZJM-20 周期式搅拌球磨机、浮选采用XFD 单槽浮选机。粗选条件试验流程图见图1。
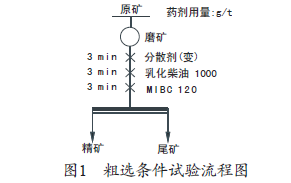
2 结果与讨论
2.1 磨矿细度试验
试验中不加分散剂,捕收剂乳化柴油用量为1000 g/t,起泡剂甲基异丁基甲醇(MIBC)用量为120 g/t,探索磨矿细度对浮选指标影响,结果见图2。
由图2 可看出,随着磨矿细度-0.074 mm 含量的增加,固定碳含量逐渐升高,-0.074 mm 含量占92.5%时固定碳含量达到最大,回收率在-0.074 mm 含量占90% 时达到最大,综合考虑,-0.074 mm 含量占92.5%为最佳磨矿细度。
2.2 捕收剂用量
试验捕收剂柴油在水中分散性不好,应乳化后再使用,在水介质中乳化柴油的小油珠粒径可达几微米甚至纳米级别,为柴油与微细粒隐晶质石墨作用创造了更好条件。磨矿细度-0.074 mm 含量为92.5%,不添加分散剂,起泡剂MIBC 用量为100 g/t,矿浆质量分数为10% 时,精矿固定碳含量、回收率随乳化柴油用量变化见图3。
由图3 可知,随着乳化柴油用量的增加,精矿固定碳含量略有降低,而回收率大幅提高,当乳化柴油用量为1000 g/t 时达到最大值,继续增加乳化柴油用量回收率开始下降。这主要是因为乳化柴油用量增加时,乳化柴油由于疏水力作用逐步在隐晶质石墨表面吸附展开,进一步提高隐晶质石墨疏水性,使更多的隐晶质石墨上浮,回收率逐渐增加,当乳化柴油用量大于1000 g/t 时,乳化柴油用量过多引起消泡,造成回收率有一定的下降。故乳化柴油最佳用量为1000 g/t。
2.3 起泡剂MIBC 用量试验
用松醇油(2# 油)、丁基醚醇、MIBC 3 种常用起泡剂浮选隐晶质石墨时,MIBC 形成的矿化泡沫稳定性好,选择性较好,且用量低,精矿回收率高,故选择MIBC 为起泡剂。磨矿细度-0.074 mm 含量为92.5%,不加分散剂,乳化柴油用量为1000 g/t,矿浆质量分数为10% 时,考察起泡剂MIBC 用量对精矿固定碳含量、回收率的影响,结果见图4。
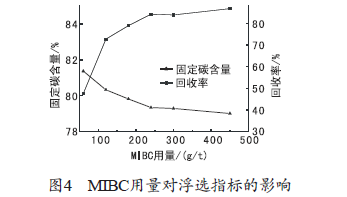
由图4 可知,精矿固定碳含量随着起泡剂增加逐渐降低,回收率大幅提高。当MIBC用量为240 g/t 时,回收率达到85%,但精矿固定碳含量下降明显,故后续MIBC 用量以120 g/t 为宜。起泡剂用量增大导致含水泡沫量增大,精矿水回收率增大,精矿固定碳含量降低,说明泡沫对脉石矿物的夹带是影响隐晶质石墨浮选指标的重要因素,在保证一定回收率的情况下起泡剂用量宜少。
2.4 分散剂种类及用量试验
由于隐晶质石墨和脉石矿物的嵌布粒度较细,为了单体解离,通常需要细磨,这导致矿浆中容易产生大量微细粒的脉石矿物,一方面,细泥对药剂吸附力增强,药剂的选择性变坏;另一方面,细泥容易粘附在正常粒度的石墨表面,形成亲水泥膜,使其可浮性变差。因此,加强对脉石矿物的抑制与分散,是改善隐晶质石墨浮选条件的途径之一。
六偏磷酸钠、羧甲基纤维素钠(CMC)、水玻璃是3 种常用的脉石矿物抑制剂,同时也是良好的分散剂。水玻璃是以水中存在的HSiO3-、H2SiO3 等亲水离子及胶粒吸附在矿粒表面,使矿粒表面电位和水化膜增大而起抑制和分散作用。当六偏磷酸钠和CMC 吸附在颗粒表面时除了增大矿物的的亲水性和表面电位的绝对值以外,还会产生空间位阻效应,强化其对脉石矿物的抑制和分散作用。
磨矿细度-0.074 mm 含量为92.5%,乳化柴油用量为1000 g/t,MIBC 用量为120 g/t 时,考察分散剂对精矿固定碳含量、回收率的影响,试验流程见图1,试验结果见图5。
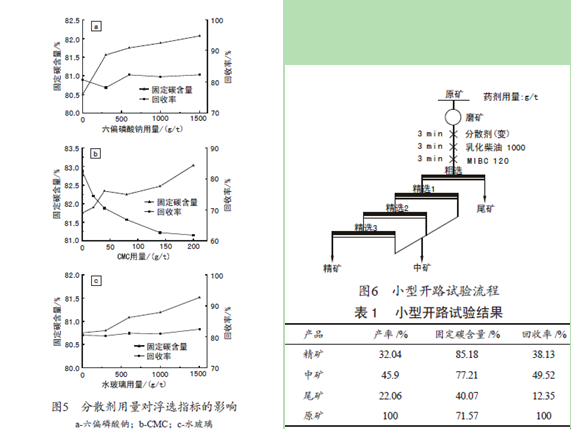
从图5 可看出,六偏磷酸钠、CMC、水玻璃用量的增大都会提高隐晶质石墨精矿固定碳含量,其中CMC 对精矿固定碳含量提高最大,固定碳含量从81.75% 升至83.03%,但其使隐晶质石墨回收率从82.49% 降低至61.86%,回收率下降的幅度最大,说明CMC 的抑制作用很强,不仅抑制脉石矿物,用量过大时也会抑制隐晶质石墨;六偏磷酸钠和水玻璃在用量为1500 g/t 时,精矿固定碳含量分别为82.07% 和81.51%,它们在有效提高固定碳含量的同时,对回收率影响不大,试验中使用六偏磷酸钠精矿指标最好,故最佳的分散剂为六偏磷酸钠。
2.5 开路流程试验
在条件试验的基础上,确定了该矿石浮选的最佳浮选药剂制度和工艺参数。选用六偏磷酸钠作为分散剂,经1 次粗选3 次精选的开路试验,将固定碳含量提高至85% 以上。具体工艺流程见图6,试验结果见表1。
3 结论
(1)隐晶质石墨原矿固定碳含量为71.57%,矿物晶粒细小,多以集合体形式出现,脉石矿物石英、绢云母等与隐晶质石墨紧密镶嵌、共生关系复杂、粒度细小,这是隐晶质石墨较难选的原因之一。
(2)条件试验结果表明,隐晶质石墨最佳的磨矿细度为-0.074 mm 含量占92.5%,最佳药剂用量为捕收剂乳化柴油1000 g/t,起泡剂MIBC 120 g/t,分散剂六偏磷酸钠1500 g/t。
(3)经过1 次粗选3 次精选的开路试验可获得两种产品,固定碳含量为85.18% 的精矿可作为牌号为W85 产品,回收率为38.13%;固定碳含量77.21% 的中矿可作为产品牌号W75 的产品,回收率为49.52%,两种产品的综合回收率为87.65%。
►欢迎进入【粉体论坛】
|