造成石英尾砂无法有效利用的根本原因在于其中含有大量的杂质矿物,无法满足目标市场的需求。因此,研究石英尾砂的深度提纯技术,实现石英同杂质矿物的有效分离,提高其内在品质是解决石英尾砂综合利用的先决条件。根据工艺矿物学研究结果,结合JG-400硅微粉内在质量指标的要求,深度提纯工艺采用“磁选—擦洗—脱泥(药)—浮选”的原则流程进行。
试验结果表明:随磁场强度的增加,精砂中Fe
2O
3含量逐渐降低,但场强大于5000后变化不大,试验选择的磁场强度为5000×80A/m。
3.2 介质擦洗试验
擦洗作业可分散泥质及其胶结物,有利于矿物的单体解离;并可促使矿物表面薄膜胶结物的分离,使其露出新鲜表面,解除不同矿物之间因长期共生而存在的“表面趋同效应”,有利于药剂的选择性吸附;试验采用加介质擦洗,通过介质同部分杂质矿物的溶解反应,加快了擦洗进程,有利于提高石英精砂的质量。擦洗试验条件及结果见表4。
表4 介质擦洗试验条件及结果
擦洗介质用量(kg/t) |
精砂指标(%) |
绝对产率 |
SiO2 |
Al2O3 |
Fe2O3 |
23.81 |
93.14 |
99.35 |
0.11 |
0.0048 |
31.74 |
92.78 |
99.53 |
0.085 |
0.0046 |
39.68 |
92.76 |
99.54 |
0.083 |
0.0045 |
试验结果表明,加介质擦洗效果较明显,精砂质量得到了提高,介质用量以31.74kg/t较合适,进一步增加意义不太大。
3.3 浮选试验
磁选和擦洗后的石英砂Fe
2O
3指标得到了有效控制,但SiO
2、Al
2O
3指标尚有差距,考虑到粉磨过程中污染的不可避免,本研究采用反浮选降低杂质矿物含量,提高精砂中SiO
2含量。浮选试验结果见表5。
表5 浮选试验结果
捕收剂用量
(g/t) |
浮选精砂指标(%) |
绝对产率 |
SiO2 |
Al2O3 |
Fe2O3 |
L.O.I |
—(入浮砂) |
92.78 |
99.53 |
0.085 |
0.0046 |
0.27 |
100 |
90.25 |
99.62 |
0.071 |
0.0044 |
0.19 |
125 |
88.15 |
99.71 |
0.053 |
0.0042 |
0.17 |
150 |
86.78 |
99.81 |
0.040 |
0.0035 |
0.12 |
175 |
85.90 |
99.84 |
0.036 |
0.0036 |
0.12 |
研究结果表明,浮选作业对提高SiO
2含量,降低Al
2O
3、L.O.I等杂质含量十分有效。至此,石英尾砂经“磁选—擦洗—脱药—浮选”工艺处理后,化学成份满足制备JG-400级硅微粉的质量要求。
4、硅微粉制备
试验采用非矿球磨机制备硅微粉,影响磨矿效果的因素较多,本研究主要探讨磨矿时间、矿介比、介配比对硅微粉粒度及白度指标的影响。
4.1磨矿时间影响
磨矿时间对磨矿效果的影响试验结果见图
2。
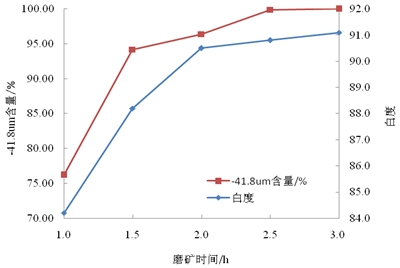
图2 磨矿时间对磨矿效果的影响
试验结果表明,在一定范围内,随磨矿时间的增加,细粒级含量及白度在不断增加;但当超过2h后,趋势明显变缓。综合考虑能耗、介质消耗、粒度及白度指标,磨矿时间以2h为宜,此时磨矿产品的白度为90.5,-41.8um累积含量为96.36%。
4.2 矿介比影响
磨矿介质是矿石磨矿过程中的能量载体和施力体,它通过磨机内磨矿介质总能量、单个磨矿介质的能量和磨矿介质的比表面积等方面的变化对磨机的生产能力、磨矿效率和粒度产生显著影响
[4]。试验考察了矿介比(指矿石加入量与磨矿介质总量的比例)对硅微粉质量指标的影响,详见图3。
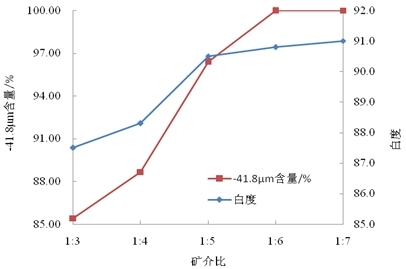
图3 不同矿介比对磨矿效果的影响曲线
试验结果表明,在一定范围内,随着矿介比的增大,磨矿产品中-41.8um粒级的含量不断增大,白度也随之提高。当矿介比增加到1:5后,增加趋势变缓,试验采用该矿介比较理想。
4.3 介配比影响
磨矿介质本身的配比是影响磨矿效率和产品粒度分布的另一个重要因素。本次试验考察了3种磨矿介质的不同配比(简称介配比)对硅微粉质量指标的影响,详见图4。
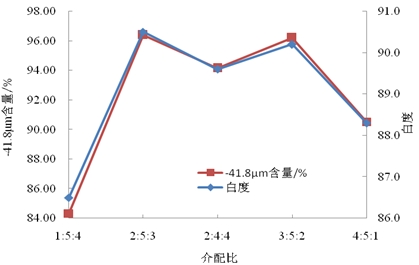
图4 介配比与硅微粉指标的关系曲线
试验结果表明,介配比对硅微粉的指标具有明显影响。当介配比为2:5:3及3:5:2时,硅微粉的粒度和白度指标出现峰值,比较而言,介配比以2:5:3最好。
5、清洗
高纯硅微粉因质纯色白,性质稳定,耐腐蚀、耐高温且具有极低的热膨胀系数,作为一种优良的无机填料广泛应用于电工电子及IT封装等行业。除上述严格的成份控制外,对其中游离的Na
+、K
+、Cl
-等离子也必须严格控制,若其含量过高,将会影响其填充产品的性能。本研究结合工艺步骤,采用去离子水对硅微粉进行“过滤—清洗”处理,试验流程见图5,试验结果见表7。
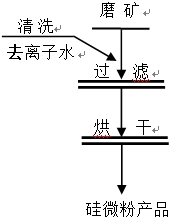
图5 “清洗—过滤”试验流程
表6“清洗—过滤”试验条件及结果
产品名称 |
化学指标(%) |
粒度指标(%) |
白度 |
水萃取液电导率(μs·cm-1) |
SiO2 |
Al2O3 |
Fe2O3 |
-41.8μm含量 |
清洗前 |
99.65 |
0.085 |
0.0045 |
96.36 |
90.5 |
42.50 |
清洗后 |
99.70 |
0.070 |
0.0036 |
96.45 |
91.2 |
8.25 |
由表7可以看出,采用“过滤—清洗”流程处理后,水萃取液最终的电导率指标为8.25μs·cm
-1,与未经去离子水清洗的硅微粉产品相比较,降低了34.25μs·cm
-1。
本研究最终硅微粉的各项理化指标检测结果见表7。
表7 JG-400电工电子级结晶硅微粉检测结果对比
项目 |
内控指标
(SJ/T10675-2002指标) |
产品实测值 |
|
|
白度 |
90.0(—) |
91.2 |
|
φ£41.8μm
(φ£39μm) |
³95%
(³75%) |
96.45% |
|
化学成分 |
SiO2(%) |
99.65 |
99.70 |
|
Fe2O3(%) |
0.010 |
0.0036 |
|
Al2O3(%) |
0.10 |
0.070 |
|
水萃取液 |
电导率(μs/cm) |
10 |
8.25 |
|
Na+(ppm) |
5 |
3.9 |
|
Cl- (ppm) |
5 |
2.6 |
|
pH |
6.5~8 |
7.5 |
|
试验结果表明,最终硅微粉达到项目研究制定的各项考核指标,满足《电子及电器工业用二氧化硅微粉》(SJ/T10675-2002) JG-400硅微粉的质量要求。
6、结语
(1)基于国内某低铁石英砂厂尾砂的矿物工艺学特性,采用“磁选—擦洗—脱泥(药)—浮选”的流程进行深度提纯,提纯后产品SiO
2=99. 81%,Al
2O
3=0.040%,Fe
2O
3=0.0035%,为用于电工电子级硅微粉提供了可能。
(2)磨矿时间、矿介比和介质配比是影响磨矿效率的关键因素,对JG-400产品的较佳粉磨条件为:磨矿时间2h,矿介比为1:5,介配比为2:5:3,硅微粉产品的-41.8μm粒度为96.36%,D
50为15.46μm,白度为90.5,满足电子级硅微粉对粒度和白度指标的要求。
(3)去离子水清洗是电子级硅微粉游离杂质离子达标的重要环节,应结合粉磨工艺安排清洗方式,降低成本。
(桂林非金属矿加工与应用技术交流会,发表于中国粉体技术杂志)