表面改性是采用物理、化学、机械等方法,根据应用需要有目的地改变粉体材料表面的物理化学性质,以满足现代新材料、新工艺和新技术发展的需求。因此,粉体表面改性技术越来越受到从事粉体加工和应用的工程技术人员的重视,在工业上的应用也越来越广泛。
粉体表面改性是集粉体加工、材料加工、材料性能、化工、机械等于一体的新技术,具有针对性或目的性强的特点,工艺方法较多,影响因素较多。因此,细致地分析这些影响因素,有助于选择正确的表面改性方法、工艺、配方和设备,从而达到预期的目的。
1、粉体原料性质
粉体原料的比表面积、粒度大小和粒度分布、比表面能、表面物理化学性质、团聚性等均对改性效果有影响,是选择表面改性剂配方、工艺方法和设备的重要考察因素之一。
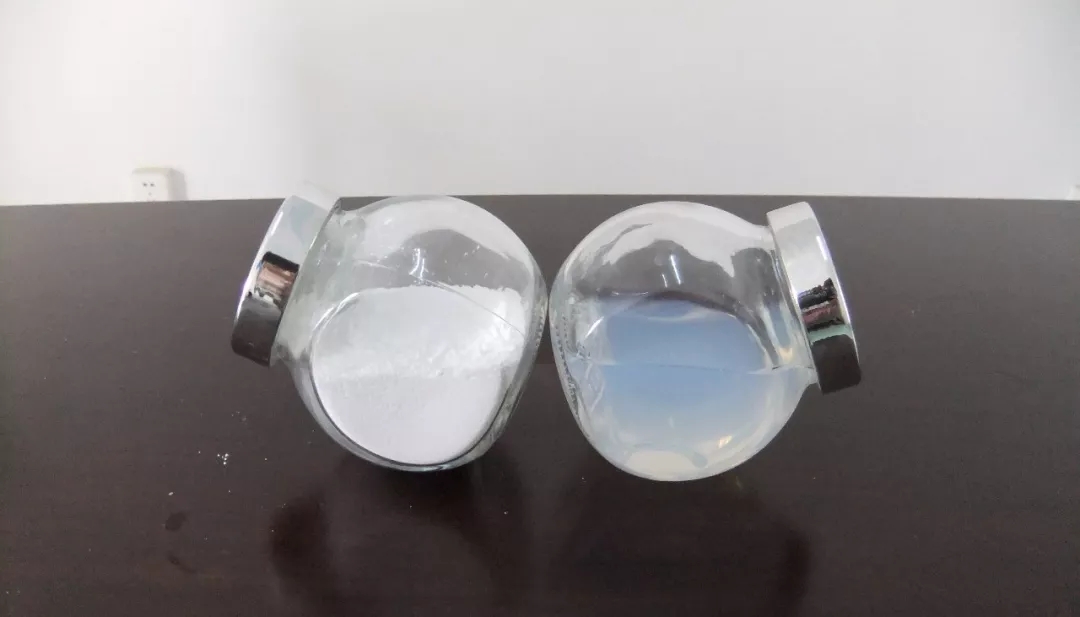
在忽略粉体孔隙率的情况下,粉体的比表面积与其粒度大小呈反比关系。即粒度越细,粉体的比表面积越大。在要求一定单分子层包覆率和使用同一种表面改性剂的情况下,粉体的粒度越细,比表面积越大,表面改性剂的用量也越大。
粉体的表面物理化学性质,如表面电性、润湿性、官能团或基团、溶解或水解特性等直接影响其与表面改性剂分子的作用,从而影响其表面改性的效果。同时,表面物理化学性质也是选择表面改性工艺方法的重要考量因素之一。
比表面能大的粉体物料,一般倾向于团聚,这种团聚体如果不能在表面改性过程中解聚,就会影响表面改性后粉体产品的应用性能。因此,团聚倾向很强的粉体最好在与表面改性剂作用前进行解团聚。
2、表面改性剂配方
粉体的表面改性在很大程度上是通过表面改性剂在粉体表面的作用来实现的。因此,表面改性剂的配方(品种、用量和用法)对粉体表面的改性效果和改性后产品的应用性能有重要影响。
表面改性剂配方具有针对性很强,即具有一把钥匙开一把锁的特点。表面改性剂的配方包括选择品种、确定用量和用法等内容。
(1)表面改性剂品种
选择表面改性剂品种的主要考虑因素是粉体原料的性质、产品的用途或应用领域以及工艺、价格和环保等因素。
粉体原料的性质主要是酸、碱性、表面结构和官能团、吸附和化学反应特性等,应尽可能选择能与粉体颗粒表面进行化学反应或化学吸附的表面改性剂,因为物理吸附在其后应用过程中的强烈搅拌或挤压作用下容易脱附。
例如,石英、长石、云母、高岭土等呈酸性的硅酸盐矿物表面可以与硅烷偶联剂进行键合,形成较牢固的化学吸附;但硅烷类偶联剂一般不能与碳酸盐类碱性矿物进行化学反应或化学吸附,而钛酸酯和铝酸酯类偶联剂则在一定条件下和一定程度上可以与碳酸盐类碱性矿物进行化学吸附作用。因此,硅烷偶联剂一般不宜用作碳酸盐类碱性矿物粉体,如轻质碳酸钙和重质碳酸钙的表面改性剂。
产品的用途是选择表面改性剂最重要的考虑因素。不同的应用领域对粉体应用性能的技术要求不同,如表面润湿性、分散性、pH值、遮盖力、耐候性、光泽、抗菌性、防紫外线等,这就是要根据用途来选择表面改性剂品种的原因之一。
例如,用于各种塑料、橡胶、胶粘剂、油性或溶剂型涂料的无机粉体(填料或颜料)要求表面亲油性好,即与有机高聚物基料有良好的亲和性或相容性,这就要求选择能使无机粉体表面疏水亲油的表面改性剂;对于陶瓷坯料中使用的无机颜料不仅要求其在干态下的有良好的分散性,而且要求其与无机坯料的亲和性好,能够在坯料中均匀分散;对于水性漆或涂料中使用的无机粉体(填料或颜料)的表面改性剂则要求改性后粉体在水相中的分散性、沉降稳定性和配伍性好。
对于无机表面改性剂则主要根据应用领域对粉体材料功能性的要求来选择,例如,要使钛白粉的耐候性和化学稳定性好,就要采用SiO2和Al2O3进行表面包覆(膜),要使白云母颜料具有良好的珠光效应就要采用TiO2进行表面包覆(膜)。
同时,不同应用体系的组分不同,选择表面改性剂时还须考虑与应用体系组分的相容性和配伍性,避免因表面改性剂而导致体系中其他组分功能的失效。
此外,选择表面改性剂时还要考虑应用时的工艺因素,如温度、压力等。所有的有机表面改性剂都会在一定的温度下分解,如硅烷偶联剂的沸点依品种不同在100~310℃之间变化。因此,所选择的表面改性剂的分解温度或沸点最好高于应用时的加工温度。
改性工艺也是选择表面改性剂的重要考虑因素之一。目前的表面改性工艺主要采用干法和湿法二种。对于干法工艺不必考虑其水溶性的问题,但对于湿法工艺要考虑表面改性剂的水溶性,因为只有能溶于水才能在湿式环境下与粉体颗粒充分地接触和反应。
例如,碳酸钙粉体干法表面改性时可以用硬脂酸(直接添加或用有机溶剂溶解后添加均可),但在湿法表面改性时,如直接添加硬脂酸,不仅难以达到预期的表面改性效果(主要是物理吸附),而且利用率低,过滤后表面改性剂流失严重,滤液中有机物排放超标。其他类型的有机表面改性剂也有类似的情况。因此,对于不能直接水溶而又必须在湿法环境下使用的表面改性剂,必须预先将其皂化、铵化或乳化,使其能在水溶液中溶解和分散。
最后,选择表面改性剂还要考虑价格和环境因素,在满足应用性能要求或应用性能优化的前提下,尽量选用价格较便宜的表面改性剂,以降低表面改性的成本。同时要注意选择不对环境造成污染的表面改性剂。
(2)表面改性剂的用量
理论上在颗粒表面达到单分子层吸附所需的用量为最佳用量,该用量与粉体原料的比表面积和表面改性剂分子的截面积有关,但这一用量不一定是100%覆盖时的表面改性剂用量,对于无机表面包覆改性,不同的包覆率和包膜层厚度可能表现出不同的特性,如颜色、光泽等。
因此,实际最佳用量的确定还是要通过改性试验和应用性能试验来确定,这是因为表面改性剂的用量不仅与表面改性时表面改性剂的分散和包覆的均匀性有关,还与应用体系对粉体原料的表面性质和技术指标的具体要求有关。
对于湿法改性,表面改性剂在粉体表面的实际包覆量不一定等于表面改性剂的用量,因为总是有一部分表面改性剂未能与粉体颗粒作用,在过滤时被流失掉了。因此,实际用量要大于达到单分子层吸附所需的用量。
(3)使用方法
表面改性剂的使用方法是表面改性剂配方的重要组成部分之一,对粉体的表面改性效果有重要影响,好的使用方法可以提高表面改性剂的分散程度和与粉体的表面改性效果,反之,使用方法不当就可能使表面改性剂的用量增加,改性效果达不到预期目的。
表面改性剂的用法包括配制、分散和添加方法以及使用二种以上表面改性剂时加药顺序。
表面改性剂的配制方法要依表面改性剂的品种、改性工艺和改性设备而定。不同的表面改性剂需要不同的配制方法,例如,对于硅烷偶联剂,与粉体表面起键合作用的是硅醇,因此,要达到好的改性效果(化学吸附)最好在添加前进行水解。
对于使用前需要稀释和溶解的其他有机表面改性剂,如钛酸酯、铝酸酯、硬脂酸等要采用相应的有机溶剂,如无水乙醇、甲苯、乙醚、丙酮等进行稀释和溶解。
对于在湿法改性工艺中使用的硬脂酸、钛酸酯、铝酸酯等不能直接溶于水的有机表面改性剂,要预先将其皂化、铵化或乳化为能溶于水的产物。
添加表面改性剂的最好方法是使表面改性剂与粉体均匀和充分的接触,以达到表面改性剂的高度分散和表面改性剂在粒子表面的均匀包覆。因此,最好采用与粉体给料速度连动的连续喷雾或滴(添)加方式,当然只有采用连续式的粉体表面改性机才能做到连续添加表面改性剂。
无机表面改性剂的配制方法比较特殊,需要考虑溶液pH值、浓度、温度、助剂等多种因素。例如,白云母表面包覆二氧化钛时,要预先将硫酸氧钛或四氯化钛进行水解。
在选用二种以上的表面改性剂对粉体进行处理时,加药顺序也对最终表面改性效果有一定影响。在确定表面改性剂的添加顺序时,首先要分析二种表面改性剂各自所起的作用和与粉体表面的作用方式(是物理吸附为主还是化学吸附为主)。一般来说先加起主要作用和以化学吸附为主的表面改性剂,后加起次要作用和以物理吸附为主的表面改性剂。
例如,混合使用偶联剂和硬脂酸时,一般来说,应先加偶联剂,后加硬脂酸,因为添加硬脂酸的主要目的是强化粉体的疏水亲油性以及减少偶联剂的用量、降低改性作业的成本。
3、表面改性工艺
表面改性剂配方确定以后,表面改性工艺是决定表面改性效果最重要的影响因素之一。表面改性工艺要满足表面改性剂的应用要求或应用条件,对表面改性剂的分散性好,能够实现表面改性剂在粉体表面均匀且牢固的包覆;同时要求工艺简单、参数可控性好、产品质量稳定,而且能耗低、污染小。
因此,选择表面改性工艺时至少要考虑以下因素:
①表面改性剂的特性,如水溶性、水解性、沸点或分解温度等;
②前段粉碎或粉体制备作业是湿法还是干法?如果是湿法作业可考虑采用湿法改性工艺;
③表面改性方法。方法决定工艺,如对于表面化学包覆,既可采用干法,也可采用湿法工艺;但对于无机表面改性剂的沉淀包膜,只能采用湿法工艺。
以下对目前采用各种有机表面改性剂对无机粉体(填料和颜料)进行表面化学改性的各种工艺的特点和适用性进行简单评述。
(1)干法工艺
干法表面改性工艺简单,适用于各种有机表面改性剂,特别是非水溶性的各种表面改性剂。在干法改性工艺中,主要工艺参数是改性温度、粉体与表面改性剂的作用或停留时间。干法工艺中表面改性剂的分散和表面包覆的均匀性在很大程度上取决于表面改性设备。
(2)湿法工艺
湿法工艺具有表面改性剂分散好、表面包覆均匀等特点,但需要后续脱水(过滤和干燥)作业,适用于各种可水溶或水解的有机表面改性剂、无机表面改性剂以及前段为湿法制粉工艺而后段又需要干燥的场合。
在湿法改性工艺中,主要工艺参数是温度、浆料浓度、反应时间、干燥温度和干燥时间等。
(3)粉碎与表面改性合二为一工艺
其特点是可以简化工艺,此外某些表面改性剂具有一定的助磨性,可在一定程度上提高粉碎效率。
不足之处是温度不好控制,难以满足改性的工艺技术要求,而且,由于粉碎过程中包覆好的颗粒不断被粉碎,产生新的表面,颗粒包覆不均匀,包覆率不高;此外,如果粉碎设备的散热不好,超细粉碎过程中局部的过高温升可能在一定程度上使表面改性剂分解或分子结构被破坏。
(4)干燥与表面改性合二为一工艺
其特点也是可以简化工艺,但干燥温度一般在200℃以上,干燥过程中加入的低沸点表面改性剂可能还来不及与与粉体表面作用就随水分子一起蒸发,在水分蒸发后出料前添加表面改性剂虽然可以避免表面改性剂的蒸发,但停留时间较短,难以确保均匀牢固的包覆。
湿法表面改性工艺虽然也要经过干燥,但是干燥之前表面改性剂已吸附于颗粒表面,排挤了颗粒表面的水化膜,因此在干燥时,首先蒸发掉的是颗粒外围的水分。
4、表面改性设备
粉体的表面改性或表面处理技术主要包括表面改性方法、工艺、表面改性剂及其配方、表面改性设备等。其中在表面改性工艺和改性剂配方确定的情况下,表面改性设备就成为影响粉体表面改性或表面处理效果的关键因素。
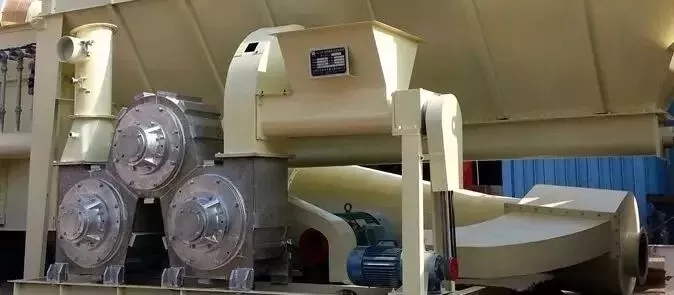
▲SLG型连续式粉体表面改性机
表面改性设备性能的优劣,不在其转速的高低或结构复杂与否,关键在于以下基本工艺特性:
①对粉体及表面改性剂的分散性;
②使粉体与表面改性剂的接触或作用的机会;
③改性温度和停留时间;
④单位产品能耗和磨耗;
⑤粉尘污染;
⑥设备的运转状态。
高性能的表面改性机应能够使粉体及表面改性剂的分散性好、粉体与表面改性剂的接触或作用机会均等,以达到均匀的单分层吸附、减少改性剂用量;同时,能方便调节改性温度和反应或停留时间,以达到牢固包覆和使溶剂或稀释剂完全蒸发(如果使用了溶剂或稀释剂);此外,单位产品能耗和磨耗应较低,无粉尘污染(粉体外溢不仅污染环境,恶化工作条件,而且损失物料,增加了生产成本),设备操作简便,运行平稳。
5、发展前景
无机粉体表面改性是应现代高技术、新材料产业,特别是功能材料产业发展而兴起的新技术,适应现代社会环保、节能、安全、健康的需求。
无机粉体表面改性产品是最具发展前景的功能粉体材料,预计未来10年市场需求量将以平均8%-10%左右的速度增长。
2018年碳酸钙精细加工应用技术提升及实操培训班
培训大纲:
1、碳酸钙粉体清洁生产技术
2、碳酸钙粉体精细加工制备技术
3、碳酸钙粉体表面改性技术开发与应用
4、碳酸钙粉体在有机聚合物材料中的应用技术
5、碳酸钙精细加工技术实操
培训咨询和交流:18301216601(微信同号)
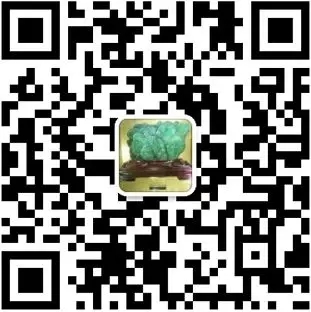
部分资料来源:影响粉体表面改性效果的主要因素,作者:郑水林
编辑整理:粉体技术网
更多精彩!欢迎扫描下方二维码关注中国粉体技术网官方微信(粉体技术网)
|